Check for power issues and ensure the water supply is connected when troubleshooting a Follett ice machine. Follett ice machines are known for their reliability and efficiency, but like any appliance, they can encounter problems.
Common issues include power supply interruptions, blocked water lines, and dirty filters. First, make sure the machine is plugged in and receiving power. Then, verify that the water supply is properly connected and flowing. Regularly cleaning and maintaining your ice machine can prevent many common problems.
If basic troubleshooting steps do not resolve the issue, consult the user manual or contact a professional technician. Proper upkeep ensures your Follett ice machine operates smoothly and efficiently, providing high-quality ice consistently.
Introduction To Follett Ice Machines
Follett Ice Machines are popular for their reliability and performance. These machines are used in various settings, providing a steady supply of ice. Whether for a small cafe or a large hospital, Follett Ice Machines meet the demand efficiently. Understanding their key features can help in troubleshooting.
Key Features Of Follett Ice Machines
Follett Ice Machines come with several impressive features. Here are some key features:
- High Production Capacity: These machines produce large amounts of ice daily.
- Energy Efficiency: Follett Ice Machines consume less energy, saving costs.
- Durable Design: Built with high-quality materials, they last longer.
- User-Friendly Interface: The controls are simple and easy to use.
Common Usage Scenarios
Follett Ice Machines are versatile, fitting into many environments. Below are some common usage scenarios:
Setting | Usage |
---|---|
Restaurants | Providing ice for drinks and food preparation. |
Hospitals | Used in patient care and medical applications. |
Hotels | Serving guests in rooms and at events. |
Office Buildings | Supplying ice for employee lounges. |
Knowing where and how these machines are used helps in understanding their importance. Follett Ice Machines are designed to cater to different needs efficiently.
Preventive Maintenance For Optimal Performance
Keeping your Follett Ice Machine in top condition is crucial. Regular maintenance ensures optimal performance. Follow these preventive tips to avoid common issues.
Regular Cleaning Protocols
Regular cleaning is essential for any ice machine. Clean the machine every two weeks.
Use a mild detergent and warm water. Clean the exterior and interior surfaces.
- Unplug the machine before cleaning.
- Remove ice from the bin.
- Wipe all surfaces with a damp cloth.
- Rinse with clean water and dry thoroughly.
Descale the machine every three months. Follow the manufacturer’s instructions.
Scheduled Inspection Checklist
A scheduled inspection helps catch potential issues early. Inspect the machine monthly using this checklist:
- Check for any unusual noises.
- Inspect the water filter for clogs.
- Ensure the ice bin is not overfilled.
- Examine the evaporator for ice buildup.
- Check the condenser coils for dust and debris.
Address any issues found during inspections promptly.
Identifying Common Issues
Follett ice machines are popular for commercial use due to their efficiency. Yet, like all machines, they can face issues. Identifying common problems early ensures they operate smoothly. Below are some common issues and how to address them.
Ice Production Inconsistencies
Ice production inconsistencies can frustrate users. Several factors contribute to this issue:
- Temperature Fluctuations: Ensure the machine is in a cool area. Extreme heat affects ice production.
- Blocked Filters: Clean or replace filters regularly. Blocked filters hinder water flow.
- Water Supply Issues: Check for any kinks in the water line. Ensure a steady water supply.
Water Leakage Problems
Water leakage can damage the machine and surrounding areas. Address these potential causes:
- Loose Connections: Tighten all water and ice connections. Loose connections often cause leaks.
- Faulty Valves: Inspect the water inlet valve. A malfunctioning valve may need replacement.
- Drainage Issues: Check the drainage system. Ensure it’s free from blockages.
Issue | Potential Cause | Solution |
---|---|---|
Low Ice Production | High Ambient Temperature | Move to Cooler Area |
No Ice Production | Clogged Filter | Clean/Replace Filter |
Water Leakage | Loose Connections | Tighten Connections |
Follett Ice Machine Troubleshooting Power Concerns
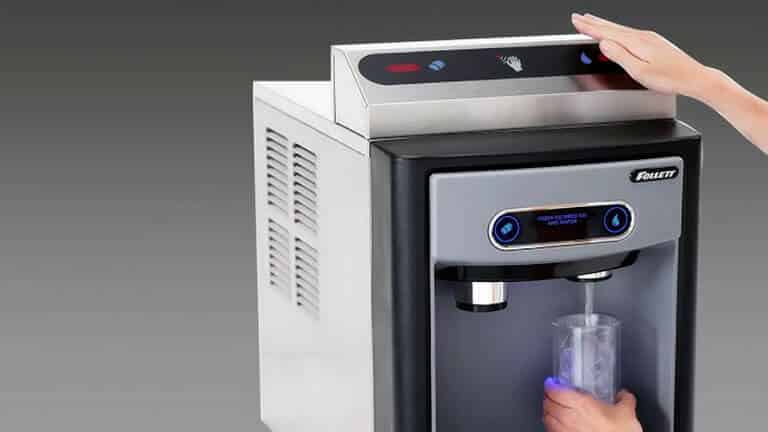
Power issues with your Follett Ice Machine can disrupt operations. Addressing these concerns promptly ensures smooth functioning. Here, we’ll guide you through some common power troubleshooting steps.
Checking Electrical Connections
Start by inspecting the machine’s electrical connections. Make sure the power cord is securely plugged into the outlet. Check for any visible damage to the cord.
- Inspect the plug for bent or broken prongs.
- Ensure the outlet is working by plugging in another device.
- Look for any signs of wear or fraying on the cord.
Next, check the circuit breaker. Sometimes, a tripped breaker can cause power loss. Reset the breaker if needed.
Resetting The Machine
If the Follett Ice Machine is still not powering on, try resetting it. Locate the reset button on the machine. Press and hold it for a few seconds.
- Turn off the machine and unplug it from the power source.
- Wait for about 5 minutes.
- Plug the machine back in and turn it on.
This simple reset often resolves minor glitches. If the machine still doesn’t power on, further troubleshooting or professional assistance may be needed.
Step | Action |
---|---|
1 | Check power cord and outlet |
2 | Inspect circuit breaker |
3 | Reset the machine |
Resolving Water Supply Complications
Water supply issues can halt your ice production. Fixing these problems quickly is crucial. This guide helps you resolve water supply complications. Let’s explore common issues like water flow and filter blockages.
Ensuring Adequate Water Flow
First, check the water supply valve. Make sure it is open. An open valve allows water to flow freely. Next, inspect the water inlet hose. It should be free of kinks and clogs. A kinked hose restricts water flow.
Another step is to check the water pressure. Low water pressure can affect ice production. Use a pressure gauge to measure it. The ideal pressure is between 20-80 psi. If the pressure is low, consider installing a booster pump.
Dealing With Water Filter Blockages
A clogged water filter can cause issues. Regularly inspect and replace the filter. Refer to the user manual for filter replacement instructions. Usually, filters need changing every six months.
To replace the filter, first, turn off the water supply. Remove the old filter and install the new one. Turn the water supply back on. Check for leaks to ensure proper installation.
Below is a simple table to help you keep track of filter replacement:
Filter Type | Replacement Frequency |
---|---|
Standard Filter | Every 6 Months |
High-Capacity Filter | Every 12 Months |
Use these steps to ensure your Follett ice machine runs smoothly. Keep water flowing and filters clean. Enjoy uninterrupted ice production.
Fixing Ice Clumping And Jamming
Is your Follett ice machine causing trouble with ice clumping and jamming? Follow these simple steps to resolve these issues. Learn how to adjust the ice thickness and clear the chute and bins effectively.
Adjusting The Ice Thickness
Ice clumping often happens due to incorrect ice thickness settings. Adjust the settings to ensure perfect ice.
- Locate the ice thickness adjustment knob on the machine.
- Turn the knob to the desired thickness setting.
- Make small adjustments and test the ice consistency.
Proper ice thickness prevents clumping and ensures smooth operation.
Clearing The Chute And Bins
Ice can jam if the chute and bins are blocked. Clear these areas to keep ice flowing smoothly.
- Turn off the ice machine and unplug it.
- Remove any ice blocking the chute and bins.
- Use warm water to melt stubborn ice clumps.
- Dry the chute and bins thoroughly before restarting the machine.
Regular cleaning prevents jams and maintains optimal performance.
Temperature Regulation Tips
Maintaining the right temperature is crucial for your Follett ice machine. Proper temperature regulation ensures optimal performance and longevity. This section covers essential tips for calibrating thermostats and monitoring ambient conditions.
Calibrating Thermostats
To keep your ice machine working well, calibrate the thermostat correctly. Follow these steps:
- Locate the thermostat inside the ice machine.
- Use a thermometer to check the current temperature.
- Adjust the thermostat to match the desired temperature.
- Wait for a few minutes and check the temperature again.
- Repeat the process until the temperature is accurate.
Regular calibration helps in maintaining consistent ice production. Ensure the thermostat is clean and free from dust. A clean thermostat performs better and lasts longer.
Monitoring Ambient Conditions
Ambient conditions affect the ice machine’s performance. Keep an eye on the surrounding environment:
- Maintain a cool room temperature.
- Ensure proper ventilation around the ice machine.
- Keep the machine away from heat sources like ovens.
- Avoid placing the machine in direct sunlight.
Ideal ambient conditions enhance the ice production efficiency. Regularly check the room temperature and adjust if needed. Keep the machine in a well-ventilated area for best results.
When To Seek Professional Help
Troubleshooting your Follett ice machine can often resolve minor issues. Yet, there are times when professional assistance is necessary. Knowing these moments can save time and prevent further damage.
Signs Of Major Component Failure
Major component failures often present clear signs. Recognizing them early can prevent extensive damage. Here are key indicators that you should contact a professional:
- Unusual noises: Grinding or loud clanking sounds indicate serious issues.
- Electrical issues: Flickering lights or frequent tripping of breakers signal electrical faults.
- Water leakage: Constant leaks suggest problems with internal components.
- Ice quality: Poor ice production or misshaped ice points to internal malfunctions.
Finding Authorized Service Providers
Choosing the right service provider is crucial. Here’s how to find authorized Follett service providers:
- Check the Follett website: The official site lists certified technicians.
- Read reviews: Look for feedback from other users about service quality.
- Verify credentials: Ensure the provider is certified by Follett.
- Compare quotes: Get estimates from multiple providers to find the best deal.
Here is a quick reference table to summarize:
Issue | Action |
---|---|
Unusual noises | Contact a professional immediately |
Electrical issues | Get an electrician or service provider |
Water leakage | Consult a technician |
Poor ice quality | Seek professional help |
Knowing when to seek professional help can save your ice machine. Ensure you contact authorized service providers for the best results.
Frequently Asked Questions
Why Is My Follett Ice Machine Not Making Ice?
Your Follett ice machine may not make ice due to a clogged water filter or low water pressure.
How Do I Reset My Follett Ice Machine?
To reset your Follett ice machine, press and hold the reset button for 10 seconds.
Why Is My Follett Ice Machine Noisy?
A noisy Follett ice machine might have a loose fan or a clogged condenser.
How Often Should I Clean My Follett Ice Machine?
Clean your Follett ice machine every 6 months to ensure optimal performance and hygiene.
What Does An Error Code On My Follett Ice Machine Mean?
An error code indicates specific issues like sensor failures or water supply problems. Refer to the manual for details.
Conclusion
Regular maintenance ensures your Follett ice machine runs smoothly. Address issues promptly to avoid downtime. Use this guide for quick troubleshooting. Keep your machine in top condition to enjoy consistent ice production. Proper care extends the lifespan and efficiency of your ice machine.
Happy troubleshooting!