Ice O Matic ice machines may face issues like not making ice or producing small ice cubes. Address these problems by checking water supply and cleaning filters.
Ice O Matic ice machines are essential for businesses that rely on a steady supply of ice. Proper maintenance and troubleshooting are crucial to ensure they function efficiently. Common issues include the machine not making ice, producing small ice cubes, or having slow ice production.
These problems often stem from water supply issues, clogged filters, or dirty condenser coils. Regular cleaning and timely inspections can prevent most of these issues. Understanding how to troubleshoot your Ice O Matic ice machine can save time and money, ensuring your business runs smoothly without interruptions.
Introduction To Ice O Matic Ice Machines
Ice O Matic ice machines are popular in many businesses. They provide reliable ice production. These machines are known for their durability and efficiency. Proper care ensures they work well for years.
The Importance Of Proper Maintenance
Maintaining your Ice O Matic machine is vital. Regular cleaning helps the machine run smoothly. It also prevents ice contamination. Follow the manufacturer’s cleaning schedule. Use approved cleaning agents. Always check the water filter. Replace it when needed. This prevents blockages and ensures clean ice.
Common Issues Faced By Users
Users often face a few common problems. Knowing these can save time and money.
- Machine Not Making Ice: Check if the power is on. Ensure water supply is connected.
- Ice Quality Issues: Clean the machine regularly. Check for any blockages in the water line.
- Unusual Noises: Inspect for loose parts. Tighten any loose screws or bolts.
Problem | Possible Cause | Solution |
---|---|---|
Not Making Ice | Power issue or no water supply | Check connections |
Bad Ice Quality | Dirty machine or blocked water line | Clean machine, check water line |
Noises | Loose parts | Tighten screws/bolts |
Identifying Common Problems
Ice O Matic ice machines can sometimes face issues. Identifying these problems early helps maintain efficiency. Here are some common problems you might encounter.
Machine Not Producing Ice
One of the most common issues is no ice production. This can be due to:
- Power supply issues – Ensure the machine is plugged in and switched on.
- Water supply problems – Check if the water supply is connected and flowing.
- Clogged filters – Clean or replace the filters regularly.
- Faulty thermostat – The thermostat may need adjustment or replacement.
Ice Quality Issues
If the ice is cloudy or has a strange taste, check for these problems:
- Dirty water filter – Replace the filter to ensure clean water.
- Mineral buildup – Clean the machine to remove any mineral deposits.
- Improper temperature settings – Adjust the temperature to the correct setting.
Unusual Noises During Operation
Strange noises can indicate different issues. Common causes include:
- Loose parts – Check for any loose screws or components.
- Faulty fan motor – A noisy motor might need repair or replacement.
- Blockages – Ensure there are no ice blockages inside the machine.
Problem | Possible Cause | Solution |
---|---|---|
No Ice Production | Power supply issues | Ensure the machine is plugged in and switched on. |
Cloudy Ice | Dirty water filter | Replace the filter. |
Unusual Noises | Loose parts | Check and tighten any loose screws or components. |
Quick Fixes For Non-technical Issues
Ice O Matic ice machines are reliable. Sometimes, they face minor issues. These issues can be easily fixed without technical knowledge. Here are some quick fixes you can try at home.
Cleaning The Machine
Ice machines need regular cleaning. Dirt and grime can cause problems. Follow these steps to clean your machine:
- Turn off the ice machine.
- Remove the ice bin.
- Use a soft cloth to wipe the inside.
- Mix a solution of water and mild detergent.
- Scrub the machine with the solution.
- Rinse with clean water.
- Dry with a clean towel.
- Replace the ice bin.
Resetting The Ice Machine
Sometimes a simple reset solves the issue. Follow these steps to reset your Ice O Matic ice machine:
- Turn off the machine.
- Unplug it from the power source.
- Wait for 10 minutes.
- Plug it back in.
- Turn the machine on.
This should reset the internal system. It often fixes minor glitches.
Adjusting Room Temperature
Room temperature can affect ice production. Ensure the room is cool. Follow these tips to adjust the room temperature:
- Keep the room temperature between 50°F and 90°F (10°C and 32°C).
- Avoid placing the machine near heat sources.
- Ensure proper ventilation around the machine.
Proper room temperature helps the machine work efficiently.
Electrical Components Ice O Matic Ice Machine Troubleshooting
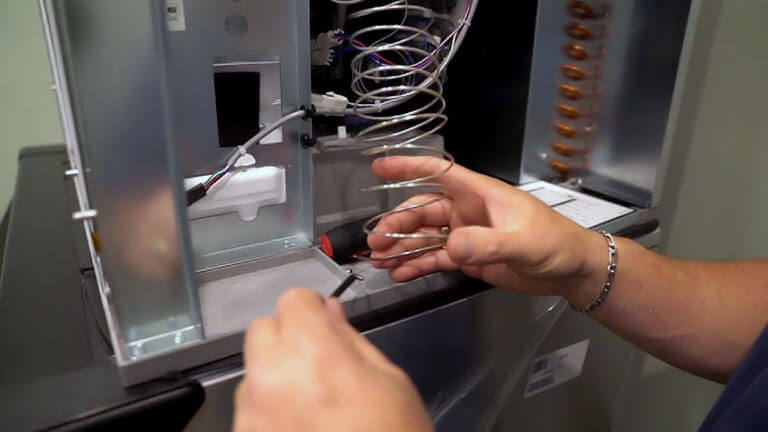
When your Ice O Matic ice machine stops working, electrical issues are often the cause. Troubleshooting these problems can get your machine running again. Focus on power supply checks and control board diagnostics to identify the problem.
Power Supply Checks
Start by checking the power supply. Ensure the machine is plugged in securely. Verify that the outlet works by plugging in another device. If the outlet is functional, move on to the machine’s power cord. Look for any signs of wear or damage.
Use a multimeter to check the voltage. Set the multimeter to the appropriate voltage setting. Place the probes on the power cord terminals. A reading that matches the machine’s specifications means the power supply is fine.
Step | Action |
---|---|
1 | Plug in securely |
2 | Verify outlet functionality |
3 | Inspect power cord |
4 | Check voltage with multimeter |
Control Board Diagnostics
The control board is the brain of your ice machine. If the machine has power but isn’t working, the control board may be the issue. Begin by inspecting the control board for visible damage. Burn marks or broken components are red flags.
Next, test the control board components. Use a multimeter to check the continuity of fuses and relays. Make sure to follow the manufacturer’s instructions. Replace any faulty components you find.
- Inspect for visible damage
- Test fuses and relays
- Replace faulty components
If the control board appears fine, reset it. Turn off the machine and unplug it. Wait a few minutes, then plug it back in and restart. This simple reset can sometimes solve complex issues.
Water-related Fixes
Ice O Matic ice machines need clean water to work well. Water problems can stop your machine from making ice. This section will help you fix water issues. Follow these steps to keep your ice machine running smoothly.
Inspecting Water Filters
Your ice machine has a water filter. Check the filter for dirt. A dirty filter stops water from flowing. Replace the filter if it looks dirty. Use the table below to know when to check your filter.
Usage Frequency | Check Filter |
---|---|
Daily | Monthly |
Weekly | Quarterly |
Solving Water Flow Problems
Water flow issues can stop ice production. First, check the water supply valve. It should be fully open. Next, inspect the water lines. Look for kinks or bends. Straighten any bent lines. If the lines are damaged, replace them.
Below are steps to solve common water flow problems:
- Ensure the water supply valve is open.
- Inspect water lines for kinks or bends.
- Straighten or replace damaged water lines.
- Check for leaks in the water lines.
- Ensure the water pressure is adequate.
By following these steps, you can solve most water flow problems. This will help your ice machine make ice again.
Mechanical Parts Maintenance
Maintaining the mechanical parts of your Ice O Matic ice machine ensures smooth operation. Regular check-ups prevent unexpected breakdowns and keep your ice machine efficient. Below, we delve into crucial areas of maintenance.
Evaporator And Condenser Issues
The evaporator and condenser are vital components. They need regular cleaning to function well. Dirty evaporators can reduce ice production. Use a soft brush to remove dirt and debris.
The condenser should be dust-free. Dust blocks airflow and causes overheating. Clean the condenser fins with a vacuum or compressed air. Make sure not to damage the fins while cleaning.
Ice Ejection Troubles
Ice ejection troubles often arise from the ejection mechanism. Check for any ice blockages. Blockages can stop ice from ejecting properly. Clear any ice build-up around the ejection arm.
Inspect the ejection arm for wear and tear. A damaged arm may need replacement. Lubricate the moving parts with food-grade silicone spray. This ensures smooth operation.
Keep these mechanical parts well-maintained. Your Ice O Matic ice machine will run efficiently.
When To Seek Professional Help
Troubleshooting an Ice O Matic ice machine can sometimes be straightforward. Yet, there are moments when seeking professional help is crucial. Knowing when to call a professional can save you time and money. It also ensures your machine is fixed correctly.
Warranty And Professional Services
Ice O Matic ice machines often come with a warranty. This warranty covers specific repairs and replacements. If your machine is still under warranty, contact a professional. Trying to fix it yourself might void the warranty.
Professional services ensure that the repair is done correctly. Professionals have the right tools and knowledge. They can also identify issues that you might miss.
Warranty Status | Action |
---|---|
Under Warranty | Contact a professional |
Out of Warranty | Consider professional help for complex issues |
Recognizing Complex Issues
Not all ice machine problems are simple. Some issues require expert knowledge. Here are signs that you need professional help:
- Unusual noises from the machine
- Ice machine not producing ice
- Water leaks around the machine
- Frequent error codes on the display
These issues often indicate deeper problems. A professional can diagnose and fix these issues. Attempting to fix them yourself might lead to more damage.
Recognizing complex issues early can prevent further damage. It also ensures your ice machine runs smoothly.
Preventive Measures And Best Practices
Keeping your Ice O Matic ice machine in top condition is crucial. Follow some preventive measures and best practices. This will ensure smooth operation and long-lasting performance. Below are detailed guidelines on maintaining your ice machine.
Regular Maintenance Schedule
Creating a regular maintenance schedule is essential. It helps in avoiding unexpected breakdowns.
- Check the machine’s filters monthly.
- Clean the ice bin every week.
- Inspect the water lines for leaks bi-weekly.
Using a maintenance log can be very helpful. It keeps track of all your maintenance activities. This ensures nothing is overlooked.
Task | Frequency |
---|---|
Filter Check | Monthly |
Ice Bin Cleaning | Weekly |
Water Line Inspection | Bi-weekly |
Operating Tips For Longevity
Following operating tips can extend the life of your ice machine. Below are some tips:
- Place the machine in a well-ventilated area.
- Keep the ambient temperature between 50-90°F.
- Use only filtered water to make ice.
Always avoid overloading the machine. This can strain the components. Also, perform a deep cleaning every three months. This removes any mineral build-up. It ensures the machine works efficiently.
Regularly check for unusual noises. This can indicate potential issues. Address them promptly to avoid costly repairs.
Frequently Asked Questions
Why Is My Ice O Matic Not Making Ice?
Check the water supply, filter, and ensure the machine is level.
How Do I Reset My Ice O Matic?
Locate the reset button, press and hold for 5 seconds.
What Causes Ice O Matic To Stop Working?
Common issues include clogged filters, faulty water lines, or electrical problems.
How Often Should I Clean Ice O Matic?
Clean every 6 months or as per manufacturer’s guidelines.
Why Is My Ice O Matic Making Small Ice Cubes?
Inspect water pressure and check for any blockages in the water line.
Conclusion
Regular maintenance can prevent many issues with your Ice O Matic ice machine. Follow these troubleshooting steps for smooth operation. Addressing minor problems early can save time and costs. Keep your ice machine in top shape for reliable performance. Always consult your user manual for specific guidance and professional support when needed.