Lochinvar boiler troubleshooting often involves checking error codes and ensuring proper maintenance. Regular inspection and timely repairs can prevent most issues.
Lochinvar boilers are known for their efficiency and reliability in heating systems. Yet, like any mechanical system, they can face problems. Common issues include ignition failure, inadequate heating, and error codes. Understanding these problems and how to address them can save time and money.
Routine maintenance and timely troubleshooting are crucial for optimal performance. Regularly inspect components, clean filters, and check connections. Addressing minor issues promptly can prevent major breakdowns. This guide provides practical tips for diagnosing and fixing common Lochinvar boiler problems.
Introduction To Lochinvar Boilers
Lochinvar boilers are a top choice for homes and businesses. They offer high efficiency and consistent performance. Many rely on them for heating and hot water needs.
Popularity And Reliability
Lochinvar boilers are popular for their advanced technology. They provide reliable heating solutions. Users appreciate their long-lasting performance and energy efficiency. These boilers are designed to reduce energy costs. They also minimize environmental impact.
Common Models And Applications
Lochinvar offers a range of models for various applications. Below is a table of some common models and their uses:
Model | Application |
---|---|
Knight XL | Large homes and commercial buildings |
Solution | Residential homes |
Armor | Industrial and commercial facilities |
FTXL | High-demand residential and light commercial |
Each model serves a unique purpose. This ensures a perfect fit for every need. Lochinvar boilers are versatile and efficient. They meet the requirements of various heating systems. This adaptability makes them a preferred choice. They are suitable for both small and large-scale applications.
Below is a list of key features of Lochinvar boilers:
- High energy efficiency
- Advanced control systems
- Durable construction
- Wide range of capacities
These features enhance the user experience. They also ensure long-term reliability and performance. Lochinvar boilers are a smart investment for any property.
Identifying Common Issues
Lochinvar boilers are reliable. Sometimes, they can have problems. Knowing these issues helps fix them quickly.
Ignition Failures
Ignition failures mean the boiler won’t start. This can be frustrating. Here are common causes:
- Faulty Igniter: The igniter may be broken.
- Gas Supply Issues: No gas means no ignition.
- Blocked Burners: Dirt can block burners.
- Thermostat Problems: A bad thermostat can stop ignition.
Check these parts first. Fixing them often resolves ignition problems.
Water Heating Inconsistencies
Water should heat evenly. If not, you may notice cold spots. Common reasons include:
- Thermostat Settings: Incorrect settings can cause uneven heating.
- Air in System: Air bubbles can disrupt water flow.
- Scale Build-Up: Minerals can clog pipes.
- Pump Issues: A faulty pump can cause poor circulation.
Adjust the thermostat. Bleed air from the system. These steps can solve the problem.
Strange Noises
Strange noises can be alarming. They often indicate a problem. Common noises include:
- Banging: This may be from trapped air or scale build-up.
- Whistling: Often caused by a high pressure.
- Humming: Could be a sign of electrical issues.
- Gurgling: May indicate air in the system.
Identify the noise type. This helps pinpoint the cause. Fixing the root cause often stops the noise.
Issue | Common Causes |
---|---|
Ignition Failures | Faulty Igniter, Gas Supply Issues, Blocked Burners, Thermostat Problems |
Water Heating Inconsistencies | Thermostat Settings, Air in System, Scale Build-Up, Pump Issues |
Strange Noises | Banging, Whistling, Humming, Gurgling |
Initial Diagnostic Steps
Troubleshooting a Lochinvar boiler can seem daunting. With the right steps, it gets easier. The first step involves initial diagnostics. Follow this guide to identify and fix issues quickly.
Safety Precautions
Before starting, ensure safety. Turn off the boiler and disconnect the power. Wear protective gloves and goggles. Check the area for gas leaks. If you smell gas, ventilate the area immediately.
Basic Inspection
Start with a visual inspection. Check for any obvious signs of damage. Look for loose wires or broken components. Ensure that the thermostat settings are correct. Inspect the water level in the boiler. Make sure it’s within the recommended range.
Component | Action |
---|---|
Wires | Check for looseness or damage |
Thermostat | Verify settings |
Water Level | Ensure it’s within range |
When To Call A Professional
If basic steps don’t fix the issue, call a professional. Complex issues need an expert’s touch. Problems like gas leaks or faulty wiring should be handled by trained technicians. Don’t risk safety by attempting complex repairs yourself.
Common signs to call a professional:
- Persistent error codes
- Unusual noises
- Water leaks
- Inconsistent heating
If any of these signs appear, contact a certified Lochinvar technician.
Quick Fixes For The Homeowner
Experiencing issues with your Lochinvar boiler? Don’t worry! Many common problems have simple solutions. Here are some quick fixes you can try at home before calling a professional.
Resetting The System
Sometimes, a simple reset can resolve many boiler issues. Follow these steps:
- Locate the reset button on the control panel.
- Press and hold the button for 10 seconds.
- Wait for the boiler to restart.
If the boiler still doesn’t work, you may need further troubleshooting.
Adjusting The Thermostat
A thermostat set too low can cause heating issues. Check and adjust your thermostat:
- Ensure the thermostat is turned on.
- Set the temperature to at least 70°F (21°C).
- Wait a few minutes for the boiler to respond.
A properly set thermostat often resolves heating problems quickly.
Checking Power Supplies
Your boiler needs power to function correctly. Verify the power supplies:
Step | Description |
---|---|
1 | Check if the boiler is plugged in. |
2 | Ensure the circuit breaker is on. |
3 | Look for any blown fuses. |
If power issues persist, contact an electrician.
By following these steps, you can resolve many common Lochinvar boiler problems yourself. Always remember, safety first! If unsure, call a professional for help.
Maintenance Tips To Prevent Breakdowns
Regular maintenance of your Lochinvar boiler helps prevent unexpected breakdowns. Follow these simple tips to keep your boiler running smoothly.
Regular Cleaning
Regular cleaning of your boiler is crucial. Dust and debris can accumulate over time and affect performance.
- Clean the boiler’s exterior to remove dust and dirt.
- Inspect the vents and ensure they are clear.
- Check the burner for soot and clean it if needed.
System Flushing
Flushing your system removes sediment and impurities that clog the boiler. This ensures optimal performance and extends the boiler’s lifespan.
- Turn off the power to the boiler.
- Connect a hose to the drain valve.
- Open the valve and let the water flow out.
- Close the valve and refill the system with clean water.
Component Checks
Regularly check the components of your boiler. This helps identify potential issues before they become serious problems.
Component | Action |
---|---|
Thermostat | Ensure it’s functioning correctly. |
Pressure Relief Valve | Test to ensure it releases pressure as needed. |
Water Levels | Check and maintain proper levels. |
Paying attention to these components can prevent costly repairs.
Lochinvar Boiler Troubleshooting Specific Lochinvar Models
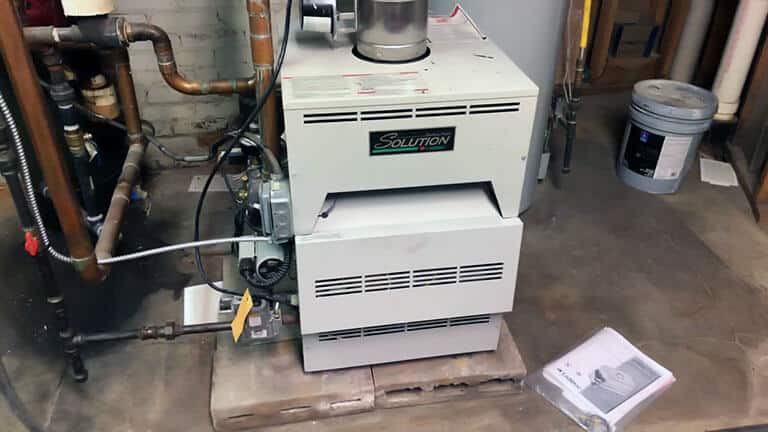
Lochinvar boilers are known for their reliability and performance. However, they can face issues that need troubleshooting. Different models have unique problems and solutions. Let’s explore the specifics of troubleshooting two popular models.
Knight Boiler Nuances
The Knight Boiler is a favorite for its efficiency. Yet, it can encounter issues. Here are some common problems and how to resolve them:
- Error Code E02: This usually indicates a problem with the fan. Check the fan wiring and connections.
- Error Code E12: This points to a flame failure. Inspect the gas supply and ensure the flame sensor is clean.
- Low Water Pressure: Ensure the system is filled to the correct pressure. Look for leaks in the system.
For a better understanding, here is a simple troubleshooting table:
Issue | Possible Cause | Solution |
---|---|---|
Error Code E02 | Fan Issue | Check fan wiring and connections |
Error Code E12 | Flame Failure | Inspect gas supply and clean flame sensor |
Low Water Pressure | System Leak | Check for leaks and refill system |
Solution Series Specifics
The Solution Series boilers are designed for ease of use. Still, they can have specific issues. Here are some common problems and their solutions:
- Error Code A03: This indicates a problem with the air pressure switch. Check the switch and its tubing.
- Error Code A16: This signals a communication fault. Inspect the control board connections.
- Temperature Fluctuations: Ensure the thermostat is functioning correctly. Inspect the temperature sensors.
For quick reference, here is a troubleshooting table:
Issue | Possible Cause | Solution |
---|---|---|
Error Code A03 | Air Pressure Switch | Check switch and tubing |
Error Code A16 | Communication Fault | Inspect control board connections |
Temperature Fluctuations | Thermostat Issue | Check thermostat and temperature sensors |
By understanding these common problems, you can ensure your Lochinvar boiler runs smoothly. Regular maintenance and prompt troubleshooting can extend the life of your boiler.
Deciphering Error Codes
Lochinvar boilers are reliable, but like all machines, they can have issues. Understanding and decoding error codes can save time and stress. This guide will help you read and fix common error codes.
Understanding The Display
The display on a Lochinvar boiler provides key information. It shows operating status, temperatures, and error codes. When an error code appears, it is important to act quickly. The display is your first line of defense.
Make sure you know how to navigate through the display menu. The user manual often has a guide for this. Familiarize yourself with the basics, so you can respond fast to any issues.
Common Codes And Solutions
Here are some common error codes and what they mean:
Error Code | Description | Solution |
---|---|---|
ERR 01 | High Limit | Check the high limit switch and reset. |
ERR 02 | Low Water | Ensure water level is adequate and refill. |
ERR 03 | Ignition Failure | Check gas supply and ignitor. |
- ERR 01: This code means the water temperature is too high. Check the high limit switch. If needed, reset it.
- ERR 02: This code indicates low water levels. Make sure the water is at the correct level. Refill if necessary.
- ERR 03: This code signals an ignition failure. Verify the gas supply. Ensure the ignitor is working.
By understanding these common codes, you can troubleshoot your Lochinvar boiler efficiently. Regular maintenance can also help prevent these errors.
Professional Repair Vs. Diy
When your Lochinvar boiler malfunctions, deciding between professional repair or DIY can be tough. Both options have their pros and cons. Understanding these can help you make the best choice.
Evaluating The Problem’s Complexity
First, assess the complexity of the issue. Some problems are easy fixes. Others require advanced skills.
- Simple issues like resetting the boiler or checking the thermostat.
- Complex issues such as gas leaks or electrical problems.
Use the boiler manual to identify the problem. If the manual doesn’t help, it’s likely a complex issue.
Benefits Of Certified Technicians
Hiring a certified technician offers many benefits. They have specialized skills and tools.
- Expertise: Certified technicians understand boiler systems well.
- Safety: They handle dangerous issues safely.
- Warranty: Professional repairs often include a warranty.
Consider these benefits before attempting a DIY fix. Professional help can save time and money in the long run.
Upgrading Your Lochinvar Boiler
Upgrading your Lochinvar boiler can enhance efficiency and reliability. Modern boilers offer advanced features and improved performance. This section will guide you on when to consider a replacement and the latest advancements in boiler technology.
When To Consider Replacement
Older boilers may become less efficient over time. Frequent breakdowns and repairs can be costly. Here are some signs it’s time to consider a replacement:
- Boiler is over 15 years old
- Energy bills are rising
- Frequent repairs are needed
- Boiler is no longer efficient
Replacing an old boiler can save you money in the long run. A new boiler can be more energy-efficient and reliable.
Advancements In Boiler Technology
Modern boilers come with many advanced features. These features can improve efficiency and user experience. Here are some notable advancements:
Feature | Benefit |
---|---|
Smart Controls | Allows remote monitoring and control |
High Efficiency | Reduces energy consumption |
Condensing Technology | Improves heat recovery |
Quiet Operation | Reduces noise levels |
Smart controls enable you to manage your boiler from your phone. High efficiency units use less energy, saving you money. Condensing technology ensures better heat recovery. Modern boilers also operate quietly, adding to comfort.
Frequently Asked Questions
Why Is My Lochinvar Boiler Not Heating?
Check the thermostat settings and power supply. Ensure the gas valve is open and the pilot light is on.
How Do I Reset My Lochinvar Boiler?
Locate the reset button on the control panel. Press and hold for a few seconds until the system restarts.
What Does A Blinking Error Code Mean?
A blinking error code indicates a specific fault. Refer to the manual for troubleshooting steps.
Why Is My Boiler Making Noise?
Noises can indicate air in the system, low pressure, or faulty components. Bleed the radiators or call a technician.
How Often Should I Service My Lochinvar Boiler?
Service your Lochinvar boiler annually to ensure efficiency and longevity. Regular maintenance can prevent major issues.
Conclusion
Troubleshooting your Lochinvar boiler can save time and money. Regular maintenance ensures efficient performance. Always refer to the user manual for guidance. Seek professional help if issues persist. A well-maintained boiler increases longevity and reliability. Stay proactive to avoid unexpected breakdowns.
Your comfort and safety are worth the effort.