To troubleshoot a Manitowoc ice machine, check for common issues like water supply problems or dirty filters. Ensure the machine is clean and properly maintained.
Manitowoc ice machines are renowned for their reliability and efficiency. Yet, like any equipment, they can encounter problems. Proper troubleshooting can save time and money. Common issues often include inadequate water supply, dirty filters, or electrical malfunctions. Regular maintenance and timely inspections can prevent most problems.
Knowing the basics of troubleshooting can help in quickly identifying and resolving issues. This guide will provide essential steps and tips to ensure your Manitowoc ice machine operates smoothly, ensuring a consistent supply of ice for your business needs.
Introduction To Manitowoc Ice Machines
Manitowoc ice machines are known for their reliability. They produce ice efficiently. Many businesses use them daily.
Popularity And Usage
Manitowoc ice machines are popular worldwide. They serve many industries. Restaurants, hotels, and hospitals rely on them. They offer various models and sizes. Each model meets different needs. They are easy to operate. They are also energy-efficient.
Importance Of Regular Maintenance
Regular maintenance keeps the machine running smoothly. It prevents unexpected breakdowns. It extends the machine’s lifespan. Regular cleaning is crucial. It prevents ice contamination. It also improves ice quality. Inspecting parts regularly helps. Replace worn-out parts immediately. This ensures the machine works efficiently.
Maintenance Task | Frequency |
---|---|
Clean the machine | Every 6 months |
Inspect parts | Monthly |
Replace filters | Annually |
Regular maintenance ensures the machine produces clean ice. It also saves on repair costs.
Common Issues Faced By Owners
Manitowoc Ice Machines are reliable. Yet, owners face common issues. This guide helps troubleshoot these problems.
Machine Not Making Ice
If your machine stops making ice, check the power supply first. Ensure the machine is plugged in. Verify the circuit breaker. If all is well, inspect the water supply. Make sure the valve is open. Clean the water filter. Replace it if necessary.
Look at the control panel. Are there any error codes? Consult the manual for code meanings. Sometimes, the machine needs a reset. Press the reset button if available.
Ice Quality Concerns
Ice quality issues often stem from water problems. Use only clean, filtered water. Impurities affect ice clarity and taste. Also, check the machine’s cleanliness. Regular cleaning prevents buildup and contamination.
If ice cubes are too small or misshapen, inspect the water inlet. Make sure it’s not clogged. Adjust the ice thickness control if needed.
Strange Noises During Operation
Strange noises can indicate different problems. A rattling sound might mean loose parts. Tighten any loose screws or panels. Grinding noises often point to motor issues. Inspect the motor and replace if needed.
If you hear a hissing sound, check for refrigerant leaks. Leaks require professional repair. Regular maintenance can prevent many of these noise issues.
Initial Diagnostic Steps
Manitowoc ice machines are reliable but can face issues. Diagnosing problems quickly helps maintain efficiency. Follow these initial diagnostic steps to identify common issues.
Visual Inspection
Start with a visual inspection of the ice machine. Check for obvious signs of wear or damage. Look for loose connections or broken parts. Ensure the machine is clean and free from debris.
Check | Details |
---|---|
Exterior | Inspect for physical damage and cleanliness. |
Connections | Ensure all connections are secure and intact. |
Components | Look for broken or worn-out parts. |
Checking Power Supply
Next, check the power supply. Ensure the machine is plugged in. Verify the outlet is working by testing with another device. Check the power cord for damage.
- Confirm machine is plugged in.
- Test outlet with another device.
- Inspect the power cord for any damage.
Assessing Water Flow
Water flow is crucial for ice production. Ensure the water supply is turned on. Check for blockages in the water line. Verify the water pressure meets the machine’s requirements.
- Turn on the water supply.
- Check water line for blockages.
- Verify water pressure is adequate.
Following these steps helps identify basic issues with your Manitowoc ice machine. Regular maintenance ensures the machine runs smoothly and efficiently.
Quick Fixes For Immediate Problems
Manitowoc ice machines are reliable. But even the best machines have issues. Knowing quick fixes can save you time and money. This section covers some easy solutions. Learn to reset the machine, clean air filters, and unclog water lines.
Resetting The Machine
Sometimes, a reset is all you need. Follow these simple steps:
- Turn off the ice machine.
- Unplug the machine from the power source.
- Wait for 5 minutes.
- Plug the machine back in.
- Turn the machine on again.
This reset can solve many minor issues. It refreshes the system and clears minor bugs.
Cleaning Air Filters
Dirty air filters can reduce efficiency. They can also cause the machine to overheat. Cleaning them is simple:
- Turn off the machine.
- Remove the front panel to access the filters.
- Take out the air filters.
- Use a vacuum or brush to clean them.
- Reinstall the clean filters.
Regular cleaning keeps the machine running smoothly. Aim to clean the filters every month.
Unclogging Water Lines
Clogged water lines can stop ice production. Here are steps to unclog them:
- Turn off the ice machine.
- Disconnect the water supply.
- Inspect the water lines for clogs.
- Use a flexible brush to clear any blockages.
- Reconnect the water supply and turn on the machine.
Unclogging water lines ensures proper water flow. This helps in producing ice efficiently.
Troubleshooting Specific Components
Manitowoc ice machines are reliable, but they can have issues. Knowing how to troubleshoot specific components can save time and money. This guide focuses on common problems with the evaporator, condenser, and sensors.
Evaporator Issues
The evaporator is crucial in making ice. Problems with the evaporator can stop ice production.
- Check for Ice Build-Up: Ice build-up can block the evaporator. Remove any excess ice.
- Inspect for Leaks: Leaks can affect the evaporator’s performance. Look for water around the unit.
- Clean the Evaporator: Dirt and grime can clog it. Use a soft brush and mild cleaner.
Condenser Complications
The condenser helps cool the machine. If it fails, the machine can overheat.
- Check the Fan: Ensure the fan is running. A broken fan can cause overheating.
- Inspect the Coils: Dirty coils can reduce efficiency. Clean them with a coil cleaner.
- Look for Blockages: Remove any debris blocking the condenser.
Sensor Malfunctions
Sensors monitor the machine’s functions. Faulty sensors can cause errors.
- Test the Sensors: Use a multimeter to check sensor readings. Replace faulty sensors.
- Check Connections: Loose wires can disrupt sensor signals. Ensure all connections are tight.
- Reset the Machine: Sometimes, a simple reset can fix sensor issues. Turn the machine off and on.
When To Call A Professional
Ice machines are crucial for many businesses. But, issues can arise. Knowing when to call a professional is key. Professionals can save time and prevent further damage. Below are key reasons to consider professional help.
Understanding Warranty Terms
Check your warranty terms before fixing your machine. Manitowoc ice machine warranties cover specific repairs. Unauthorized repairs can void your warranty. Professionals understand these terms well.
Warranty Coverage | Details |
---|---|
Parts | Covers malfunctioning parts. |
Labor | Covers repair labor costs. |
Exclusions | Does not cover wear and tear. |
Identifying Complex Issues
Some problems are not easy to spot. Complex issues need a trained eye. Professionals have the right tools. They can diagnose and fix tough problems.
- Electrical issues
- Refrigerant leaks
- Control board failures
Safety Considerations
Safety is a top priority. Ice machines use electricity and refrigerants. Handling these can be dangerous. Professionals know safety protocols. They have protective gear and training. This keeps you and your staff safe.
- Wear protective gear
- Follow safety protocols
- Use the right tools
Knowing when to call a professional can save you time. It can also save money and ensure safety. Consider these points next time your Manitowoc ice machine has issues.
Preventive Maintenance Tips
Maintaining your Manitowoc Ice Machine helps keep it running well. Here are some preventive maintenance tips. Follow these to ensure your machine works efficiently.
Regular Cleaning Schedule
Set up a regular cleaning schedule for your ice machine. Clean it at least once every six months. For high-use machines, clean it every three months.
- Turn off the machine before cleaning.
- Use a soft brush to clean the ice bin.
- Rinse all parts with warm water.
- Sanitize with a food-safe sanitizer.
Regular cleaning prevents mold and bacteria. It ensures ice quality and machine longevity.
Water Filtration Solutions
Install a water filter to improve ice quality. Filters remove impurities and extend machine life. Choose a filter compatible with Manitowoc Ice Machines.
Filter Type | Benefits |
---|---|
Carbon Filter | Removes chlorine and improves taste |
Scale Inhibitor | Prevents mineral buildup |
Replace filters every six months. Clean the filter housing regularly. This ensures effective filtration and optimal machine performance.
Upkeeping Environmental Conditions
Maintain good environmental conditions around your ice machine. Ensure proper ventilation and temperature control. Keep the machine away from heat sources.
- Place the machine in a cool, dry area.
- Ensure at least 6 inches of clearance around the machine.
- Regularly check and clean air filters.
Proper environmental conditions help the machine run efficiently. It reduces wear and tear, saving on repairs.
Advanced Manitowoc Ice Machine Troubleshooting Techniques
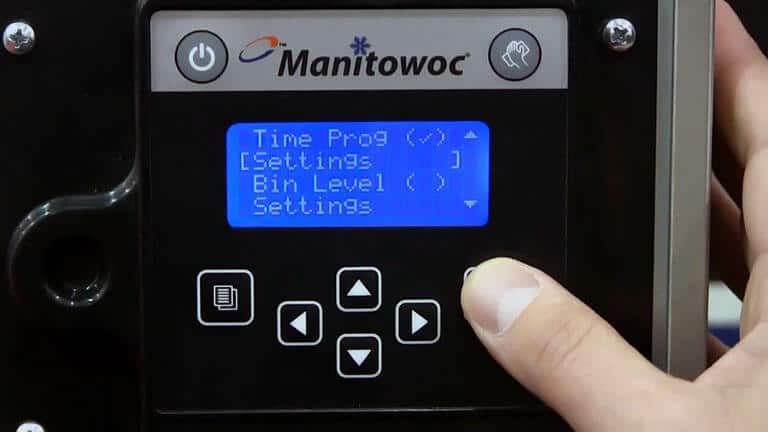
Advanced troubleshooting techniques for Manitowoc Ice Machines can save you time and money.
These techniques address complex issues beyond basic fixes. This guide will help you navigate advanced troubleshooting methods.
Interpreting Error Codes
Manitowoc Ice Machines display error codes for specific problems. Understanding these codes is crucial.
Below is a table of common error codes and their meanings.
Error Code | Description | Possible Solution |
---|---|---|
E01 | High Pressure Cutout | Check for proper ventilation. |
E02 | Low Pressure Cutout | Inspect refrigerant levels. |
E03 | Water Supply Issue | Ensure water supply is steady. |
Adjusting Settings
Properly adjusting the settings can optimize performance. Follow these steps for adjustment:
- Access the control panel.
- Navigate to the settings menu.
- Adjust the ice thickness setting.
- Set the cleaning schedule.
Regularly checking and adjusting these settings ensures efficient operation. For best results, refer to the user manual.
Firmware Updates And Resets
Keeping the firmware updated is essential. Updates fix bugs and improve performance. Follow these steps for updates:
- Visit the Manitowoc website.
- Download the latest firmware.
- Use a USB drive for installation.
- Follow on-screen instructions to complete the update.
If issues persist, a factory reset may help. Resetting can resolve many problems. To reset:
- Turn off the machine.
- Press and hold the reset button.
- Wait for the machine to reboot.
Always back up settings before resetting. This ensures you can restore your preferred configurations.
Conclusion: Ensuring Longevity And Efficiency
Keeping your Manitowoc ice machine in top shape guarantees its longevity and efficiency. Regular maintenance and timely troubleshooting can save you money and prevent bigger problems. Below, we summarize key points and provide tips for proactive care and resources for further assistance.
Summary Of Key Points
- Regularly clean and sanitize the machine to avoid build-up and contamination.
- Check for leaks and ensure proper water flow to prevent ice production issues.
- Monitor the machine’s temperature settings to ensure optimal performance.
- Replace worn-out parts promptly to avoid breakdowns.
Encouragement For Proactive Care
Proactive care extends the life of your Manitowoc ice machine. Follow a regular cleaning schedule and inspect the machine often. Address minor issues before they become major problems. This saves you time and money in the long run.
Create a maintenance log. Document each cleaning, inspection, and repair. This helps track the machine’s performance and identify recurring issues. A well-maintained machine operates efficiently and produces high-quality ice.
Resources For Further Assistance
If you need more help, consult the Manitowoc Ice Machine manual. It provides detailed troubleshooting steps and maintenance tips. You can also reach out to a professional technician for complex issues.
Resource | Contact Information |
---|---|
Manitowoc Customer Support | 1-800-545-5720 |
Authorized Service Technicians | Service Locator |
Online Troubleshooting Guide | Troubleshooting Guide |
Frequently Asked Questions
Why Is My Manitowoc Ice Machine Not Making Ice?
Your Manitowoc ice machine might not make ice due to water supply issues or a clogged filter.
How Do I Reset My Manitowoc Ice Machine?
To reset your Manitowoc ice machine, press the reset button located behind the front panel.
What Causes Manitowoc Ice Machine Freeze-ups?
Freeze-ups in Manitowoc ice machines are often caused by low water flow or a malfunctioning thermostat.
How Often Should I Clean My Manitowoc Ice Machine?
You should clean your Manitowoc ice machine every six months to ensure optimal performance and ice quality.
Why Is My Manitowoc Ice Machine Leaking Water?
Water leaks in Manitowoc ice machines usually occur due to a faulty water pump or loose connections.
Conclusion
Solving issues with your Manitowoc ice machine doesn’t have to be stressful. Follow these troubleshooting tips to keep your machine running smoothly. Regular maintenance and timely repairs can extend its lifespan. Always consult the manual or seek professional help for complex problems.
Enjoy reliable ice production with a well-maintained machine.