To troubleshoot a Pitco deep fryer, check the power supply and thermostat settings first. Then, inspect the gas or electrical connections for issues.
Pitco deep fryers are essential kitchen appliances in many commercial settings. These fryers ensure quick and consistent cooking, making them indispensable for busy kitchens. Like any equipment, they can encounter issues over time. Common problems include power supply interruptions, thermostat malfunctions, and gas or electrical connection failures.
Regular maintenance and timely troubleshooting can keep your Pitco deep fryer running smoothly. Understanding these basics helps maintain efficiency and prolongs the lifespan of your fryer. This guide offers quick and easy steps to identify and fix common issues, ensuring your deep fryer operates optimally.
Identifying Common Pitco Deep Fryer Issues
Pitco deep fryers are durable and reliable. Yet, like all machines, they can face issues. Knowing common problems helps in quick troubleshooting. This section helps identify and fix these issues.
Symptoms Of Malfunction
Recognizing the symptoms early can prevent bigger problems. Here are common signs your Pitco deep fryer might be malfunctioning:
- Inconsistent Cooking: Food is unevenly cooked or overcooked.
- Unusual Noises: The fryer makes strange sounds during operation.
- Temperature Fluctuations: The oil temperature doesn’t stay stable.
- Power Issues: The fryer won’t turn on or keeps shutting off.
- Oil Leaks: Oil is leaking from the fryer.
Frequent Error Codes
Pitco deep fryers display error codes to signal specific issues. Understanding these codes helps in quick fixes:
Error Code | Description | Possible Solution |
---|---|---|
E1 | High Limit Failure | Check and reset the high limit switch. |
E4 | Ignition Failure | Inspect the ignition module and wiring. |
E6 | Temperature Probe Failure | Replace the faulty temperature probe. |
E10 | Communication Error | Ensure all connections are secure. |
Initial Diagnostic Steps
To keep your Pitco Deep Fryer in top shape, start with initial diagnostic steps. These steps help identify common issues quickly. Follow the guide below to ensure efficient troubleshooting.
Safety Precautions
Safety is the most important part. Turn off the fryer and unplug it. Allow the unit to cool before you begin. Wear protective gloves and goggles. Keep a fire extinguisher nearby.
Equipment You’ll Need
Gather the necessary tools for troubleshooting. Having the right equipment ensures smooth inspection.
- Multimeter
- Wrench set
- Screwdrivers
- Cleaning cloth
- Replacement parts (if needed)
Tool | Purpose |
---|---|
Multimeter | Check electrical components |
Wrench set | Loosen or tighten nuts and bolts |
Screwdrivers | Remove or tighten screws |
Cleaning cloth | Wipe down components |
Replacement parts | Replace faulty parts |
Check Power Supply
- Ensure the fryer is plugged in.
- Check the outlet for power.
- Inspect the power cord for damage.
- Test the outlet with another device.
- Use a multimeter to check continuity.
Inspect The Thermostat
The thermostat regulates the temperature. Check if it is set correctly.
- Locate the thermostat dial.
- Turn the dial to a higher setting.
- Listen for a click sound.
- If no click, the thermostat might be faulty.
Examine Heating Elements
The heating elements warm the oil. Inspect them for any visible damage.
- Turn off the fryer and let it cool.
- Open the fryer to access the heating elements.
- Check for any burnt or broken parts.
- Use a multimeter to test for continuity.
- Replace if necessary.
Clean The Fryer
A clean fryer works better. Regular cleaning prevents many issues.
- Turn off and unplug the fryer.
- Let it cool completely.
- Remove and clean the baskets.
- Wipe down the interior with a damp cloth.
- Ensure all parts are dry before reassembling.
Power Problems: No Heat Or Power
Experiencing power issues with your Pitco deep fryer can be frustrating. A common problem is when the fryer has no heat or power. This issue can stem from several causes. Let’s explore some solutions to get your fryer back in working order.
Checking Electrical Connections
First, inspect the electrical connections. Ensure the fryer is plugged into a working outlet. Verify the power cord is in good condition and not damaged. A damaged cord can cause power issues.
Use a multimeter to check the voltage at the outlet. The outlet should supply the correct voltage for your fryer model. If the outlet is faulty, you may need an electrician.
Resetting The High-limit Thermostat
The high-limit thermostat prevents the fryer from overheating. If the fryer overheats, the thermostat shuts off power. Resetting the thermostat can resolve this issue.
Follow these steps to reset the high-limit thermostat:
- Turn off the fryer and unplug it.
- Locate the high-limit thermostat button. It’s usually near the control panel.
- Press the reset button firmly.
- Plug the fryer back in and turn it on.
If the fryer still has no heat or power, the thermostat might need replacement. Consult a professional for further diagnosis.
Temperature Control Challenges
Dealing with temperature control challenges in your Pitco deep fryer can be frustrating. Proper temperature regulation is crucial for maintaining food quality and safety. Addressing these issues promptly ensures your fryer operates efficiently.
Calibrating Thermostats
Incorrect thermostat calibration can cause temperature fluctuations. Follow these steps to calibrate your thermostat:
- Turn off and unplug the fryer.
- Remove the thermostat cover.
- Locate the calibration screw.
- Use a screwdriver to adjust the screw.
- Turn clockwise to increase temperature, counterclockwise to decrease.
- Plug in and test the fryer with a thermometer.
- Repeat adjustments as needed.
Regular calibration ensures accurate temperature control.
Replacing Faulty Thermopiles
A faulty thermopile can disrupt the temperature control system. Here’s how to replace a thermopile:
- Turn off and unplug the fryer.
- Remove the access panel.
- Locate the thermopile near the pilot light.
- Disconnect the thermopile wires.
- Remove the old thermopile.
- Install the new thermopile.
- Reconnect the wires.
- Replace the access panel and test the fryer.
Replacing faulty thermopiles ensures stable temperature regulation.
Oil Quality And Filtration Fixes
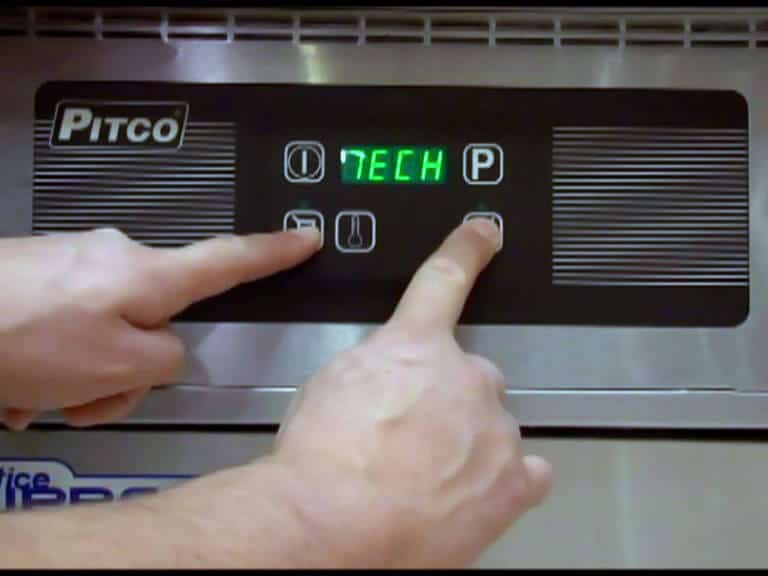
Maintaining the oil quality in your Pitco deep fryer is crucial. Good oil quality ensures tasty fried foods and prolongs the fryer’s lifespan. Understanding the filtration system and maintaining oil life can prevent many issues.
Troubleshooting The Filtration System
The filtration system removes food particles from the oil. If the system fails, oil quality drops.
- Check the filter paper: Replace if torn or clogged.
- Inspect the pump: Ensure it is not blocked or damaged.
- Examine the hoses: Look for cracks or leaks.
If the filtration system is not working, follow these steps:
- Turn off the fryer and let it cool.
- Remove and clean the filter assembly.
- Check for any food debris and clean it out.
- Reassemble the filter and test the system.
Maintaining Oil Life
Maintaining oil life is essential for quality frying. Fresh oil means better-tasting food and fewer health risks.
Follow these tips to extend oil life:
- Filter the oil daily to remove food particles.
- Store oil in a cool, dark place to prevent degradation.
- Avoid overheating the oil; keep it at the recommended temperature.
Use this table to track oil quality:
Check | Frequency |
---|---|
Filter Oil | Daily |
Change Oil | Weekly |
Inspect Filter System | Monthly |
Regular maintenance of the filtration system and oil can save costs. It also ensures consistently delicious fried foods.
Ignition Issues And Pilot Lights
Having trouble with your Pitco deep fryer? Ignition issues and pilot lights are common problems. A malfunctioning pilot light can disrupt your cooking schedule. This guide will help you troubleshoot and fix these issues.
Cleaning The Burner Orifices
The burner orifices can get clogged with grease and food particles. Regular cleaning ensures proper gas flow to the burner.
Here’s how to clean the burner orifices:
- Turn off the gas supply to your fryer.
- Remove the burner assembly carefully.
- Use a small brush to clean the orifices.
- Reassemble the burner and turn the gas back on.
Make sure the orifices are clear to avoid ignition issues.
Adjusting The Pilot Flame
A weak pilot flame can cause ignition problems. Adjusting it can ensure a consistent flame.
Follow these steps to adjust the pilot flame:
- Locate the pilot adjustment screw near the burner.
- Use a screwdriver to adjust the screw.
- Turn the screw slowly to increase or decrease the flame.
- Ensure the flame is blue and steady.
A proper pilot flame ensures reliable ignition.
Regular maintenance is key to keeping your Pitco deep fryer in top shape.
Handling Unusual Noises And Odors
Deep fryers are essential in many kitchens, providing crispy, delicious food. Sometimes, they make strange noises or emit unusual smells. Identifying and fixing these issues quickly is crucial.
Identifying The Source
Unusual noises and odors can stem from various sources. Start by checking the fryer’s heating elements. Ensure they are clean and free of debris. Dirty elements often cause popping noises.
Next, inspect the oil quality. Old or contaminated oil can emit foul odors. Replace the oil if it smells rancid or burnt. Also, check for any foreign objects in the oil. These can create unusual sounds and smells.
Examine the fryer’s ventilation system. Blockages in the vents can cause overheating and strange odors. Ensure the vents are clear and functioning properly.
Mitigating Noise And Smell
Regular cleaning is vital. Wipe down the heating elements and clean the oil tank weekly. This prevents buildup that causes noise and smell.
Use high-quality oil designed for deep fryers. Cheap oil breaks down quickly, leading to unpleasant odors. Change the oil regularly to keep it fresh.
Maintain the ventilation system. Clean the vents monthly to ensure proper airflow. This helps in preventing overheating and bad smells.
Monitor the fryer’s temperature settings. Overheating can cause oil to burn, leading to both noise and smell issues. Keep the temperature within the recommended range.
Issue | Possible Cause | Solution |
---|---|---|
Noises | Dirty heating elements | Clean elements regularly |
Noises | Foreign objects in oil | Remove objects |
Odors | Old or contaminated oil | Replace oil |
Odors | Blocked ventilation | Clear vents |
Follow these steps to keep your Pitco deep fryer running smoothly. Regular maintenance prevents most noise and smell issues.
Regular Maintenance For Optimal Performance
Maintaining your Pitco deep fryer ensures it works efficiently. Regular upkeep prevents breakdowns and extends its lifespan. Follow these tips for optimal performance.
Cleaning Schedules
Regular cleaning is crucial for your Pitco deep fryer. Stick to a daily and weekly cleaning routine for best results.
- Daily Cleaning:
- Drain and filter the oil.
- Wipe down the exterior with a damp cloth.
- Remove and clean the fry baskets.
- Weekly Cleaning:
- Deep clean the fry pot.
- Clean the heating elements.
- Check for oil buildup in hard-to-reach areas.
Part Replacements And Servicing
Replacing parts timely ensures your fryer runs smoothly. Here are key parts to monitor.
Part | Replacement Frequency |
---|---|
Oil Filters | Every 6 months |
Heating Elements | Annually |
Thermostats | Every 2 years |
Regular servicing by a professional is also essential. Schedule a service check twice a year to identify any issues early. This helps keep your fryer in top shape.
When To Call A Professional
Owning a Pitco deep fryer can be a delight. But, like any equipment, it may face problems. Knowing when to call a professional can save time and money. This section helps you decide when to seek expert help.
Assessing Repair Complexity
Some problems are simple to fix. Cleaning filters or changing oil can be done at home. But complex issues need a professional touch. Here are signs that you need expert help:
- Fryer does not heat up.
- Unusual noises during operation.
- Burner won’t ignite.
- Temperature control issues.
Attempting complex repairs can cause more damage. Always assess the problem first. If unsure, call a technician.
Finding Qualified Service Technicians
Finding the right technician is important. Look for certified Pitco service technicians. They have the knowledge and tools to fix your fryer. Here are steps to find a good technician:
- Check Pitco’s official website for certified technicians.
- Read reviews and ratings online.
- Ask for recommendations from other business owners.
- Ensure the technician provides a warranty for their work.
Using a qualified technician ensures your fryer works well. It also extends the life of your equipment.
For an easy reference, here’s a quick checklist:
Problem | Action |
---|---|
Fryer not heating | Call a professional |
Unusual noises | Call a professional |
Burner issues | Call a professional |
Temperature control | Call a professional |
Knowing when to call a professional helps you avoid bigger problems. It ensures your Pitco deep fryer runs smoothly.
Upgrading Your Pitco Deep Fryer
Upgrading your Pitco Deep Fryer can boost efficiency and performance. New models offer advanced features and improved technology. Consider the benefits before making a decision.
Considering New Models
When choosing a new Pitco deep fryer model, several factors come into play. New models often have better energy efficiency. They also feature advanced temperature controls.
Look for models with easy-to-clean components. This can save time and reduce maintenance. Improved safety features are another benefit. Modern models often include automatic shut-off and better insulation.
Model | Energy Efficiency | Safety Features | Maintenance |
---|---|---|---|
Pitco Model A | High | Automatic Shut-off | Easy-to-Clean |
Pitco Model B | Medium | Improved Insulation | Moderate |
Cost-benefit Analysis Of Upgrades
Performing a cost-benefit analysis helps in decision-making. Start by listing the upgrade costs. Include the price of the new model and installation fees.
Next, consider the benefits. These include energy savings and reduced repair costs. Improved efficiency can result in faster cooking times. This can increase customer satisfaction and revenue.
Use the table below to compare costs and benefits.
Cost | Benefit |
---|---|
Purchase Price | Energy Savings |
Installation Fees | Reduced Repair Costs |
Training | Increased Efficiency |
Weigh the costs against the benefits. If the benefits outweigh the costs, an upgrade is likely a good investment.
Frequently Asked Questions
Why Is My Pitco Deep Fryer Not Heating?
Check the thermostat and heating element. They may need replacement or recalibration.
How To Reset Pitco Deep Fryer?
Locate the reset button on the control panel. Press and hold it for a few seconds.
What Causes Pitco Fryer To Overheat?
Thermostat malfunction or blocked ventilation can cause overheating. Ensure proper airflow and check the thermostat.
How To Clean A Pitco Deep Fryer?
Drain the oil, remove debris, and use warm water with mild detergent to clean all surfaces.
Why Is Pitco Fryer Making Noise?
Unusual noises may indicate a faulty pump or motor. Inspect and replace faulty components if necessary.
Conclusion
Mastering Pitco deep fryer troubleshooting ensures smooth kitchen operations. Regular maintenance prevents common issues. Always follow manufacturer guidelines. A well-maintained fryer boosts efficiency and food quality. Keep this guide handy for quick reference. Enjoy hassle-free frying and delicious results every time.
Happy frying!