Ensure the power source is reliable and the settings are correct. Verify the press is heating evenly across the surface.
Introduction Vevor heat press machines are popular for their efficiency and versatility in transferring designs onto various materials. Despite their reliability, users may encounter issues that hinder optimal performance. Understanding common troubleshooting steps can save time and prevent frustration. Proper maintenance and regular checks ensure the machine operates smoothly.
Addressing issues like uneven heating, power supply problems, or incorrect settings can enhance the longevity of your heat press. This guide will provide essential tips to troubleshoot and resolve common problems, ensuring your Vevor heat press works effectively. By following these steps, you can maintain high-quality results and extend the life of your equipment.
Introduction To Vevor Heat Press
The Vevor Heat Press is a popular tool for creating custom designs. Professionals use it for transferring images and graphics onto various materials. This machine is essential for printing on t-shirts, mugs, hats, and more. Vevor heat presses are known for their durability and efficiency. They ensure high-quality prints with vibrant colors. Understanding how these machines work can save time and frustration. This guide will help you troubleshoot common issues.
The Importance Of Reliable Equipment
Having reliable equipment is crucial for any printing business. A dependable heat press ensures consistent, high-quality results. This minimizes errors and reduces waste. Reliable machines also enhance productivity and customer satisfaction. If your equipment fails, it can lead to delays and lost revenue. Investing in a good heat press like Vevor can prevent these problems. Reliability in equipment leads to smoother operations and happier clients.
Common Vevor Models Used By Professionals
Professionals often choose specific Vevor models for their unique features. Below is a table highlighting some popular models:
Model | Features | Best For |
---|---|---|
Vevor 5-in-1 | Multiple attachments, digital controls | Versatility, multiple projects |
Vevor 8-in-1 | Advanced attachments, larger work area | High-volume, varied projects |
Vevor Swing Away | 360-degree rotation, user-friendly | Ease of use, safety |
Each model offers unique benefits. The Vevor 5-in-1 is great for those needing versatility. It comes with multiple attachments for different projects. The Vevor 8-in-1 is perfect for high-volume operations. It includes advanced attachments and a larger work area. The Vevor Swing Away model is user-friendly and safe. Its 360-degree rotation makes it easy to use.
- Vevor 5-in-1: Ideal for versatility
- Vevor 8-in-1: Best for high-volume tasks
- Vevor Swing Away: Known for ease of use and safety
Choosing the right model depends on your needs. Each model’s features cater to different professional requirements. Understanding these differences can help you make an informed decision.
Identifying Common Issues
Heat presses, like the Vevor Heat Press, are essential for creating custom designs. But, they can sometimes face issues. Identifying these common issues helps in troubleshooting and ensures smooth operation. Below, we explore two major problems: Temperature Inconsistencies and Uneven Pressure Distribution.
Temperature Inconsistencies
Temperature inconsistencies can ruin your designs. It’s important to maintain the correct temperature. Here are some common reasons:
- Faulty Temperature Sensor: A malfunctioning sensor gives incorrect readings.
- Heating Element Issues: A damaged element heats unevenly.
- Incorrect Settings: Ensure the settings match the material requirements.
To fix these issues, check the sensor and heating element. Replace them if needed. Always double-check your settings before starting a project.
Uneven Pressure Distribution
Uneven pressure can lead to poor-quality prints. This issue usually arises due to:
- Improper Adjustment: Incorrect pressure settings cause uneven distribution.
- Worn-out Pads: Old or damaged pads can’t provide even pressure.
- Machine Alignment: Misaligned parts affect pressure consistency.
To resolve this, adjust the pressure settings properly. Replace worn-out pads. Ensure all parts are correctly aligned. Regular maintenance keeps the machine in good condition.
Quick Fixes For Heat Press Problems
Heat press machines can sometimes be tricky. Knowing quick fixes helps. This guide covers simple solutions for common issues. Follow these tips for better results.
Adjusting Temperature Controls
The right temperature is crucial. Incorrect settings cause bad transfers. Follow these steps to adjust temperature controls:
- Turn on your Vevor Heat Press.
- Locate the temperature control panel.
- Use the up and down arrows to set the desired temperature.
- Wait until the machine reaches the set temperature.
Common mistakes include setting the temperature too high or low. Always refer to the material guidelines. This ensures proper adhesion and prevents damage.
Ensuring Even Pressure
Even pressure is key for perfect transfers. Uneven pressure causes incomplete prints. Here’s how to ensure even pressure:
- Check the pressure knob on your heat press.
- Turn the knob clockwise to increase pressure.
- Turn the knob counterclockwise to decrease pressure.
- Test the pressure using a blank material first.
Make sure the pressure is even across the entire platen. Uneven pressure can result in wasted materials and time. Adjust as needed for each project.
Maintenance Tips To Prevent Downtime
Regular maintenance can keep your Vevor heat press running smoothly. It helps prevent unexpected issues and ensures long-lasting performance. Follow these tips to reduce downtime and maintain efficiency.
Regular Cleaning Routines
Cleaning your heat press regularly is crucial. Dust and debris can affect performance. Use a soft cloth to wipe down surfaces. Avoid using harsh chemicals. These can damage the machine.
- Clean the heat platen after each use.
- Inspect the silicone pad for any residue.
- Wipe the exterior with a damp cloth.
- Keep the area around the machine clean.
Periodic Inspections And Replacements
Regular inspections help identify potential issues early. Check all moving parts for wear and tear. Replace any damaged components promptly.
Component | Inspection Frequency | Replacement Frequency |
---|---|---|
Heat Platen | Weekly | Annually |
Silicone Pad | Monthly | Every 6 months |
Electrical Connections | Monthly | As needed |
Regular maintenance extends the life of your Vevor heat press. Follow these simple tips to prevent downtime and ensure smooth operation.
Vevor Heat Press Troubleshooting Electronic Components
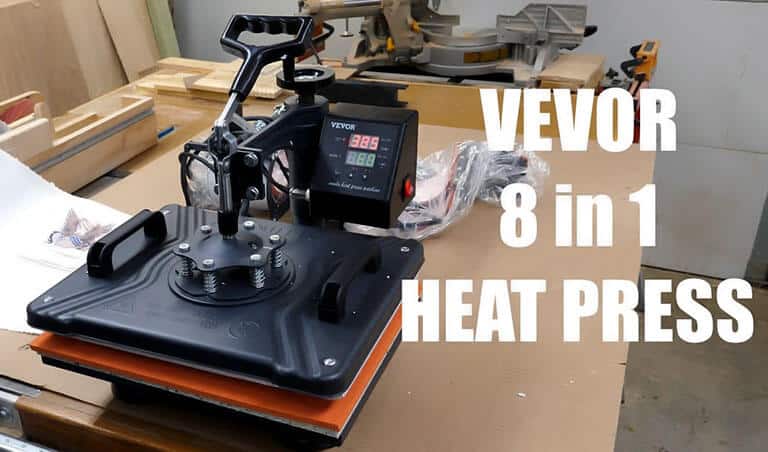
Heat press machines sometimes face electronic issues. Knowing how to fix these can save time and money. In this section, we’ll focus on solving display errors and resetting the heat press. Follow these steps to ensure your Vevor heat press works smoothly.
Solving Display Errors
Display errors can stop your heat press from working. Here are steps to fix common display issues:
- Check the power source: Ensure the machine is plugged in.
- Inspect the power cord: Look for signs of damage or wear.
- Test the outlet: Plug another device to confirm the outlet works.
- Examine the display panel: Look for loose connections or visible damage.
If the display still shows errors, it might be a board issue. Replacing the control board may be necessary. Contact Vevor support for guidance on replacing parts.
Resetting The Heat Press
Resetting your heat press can solve many electronic issues. Here are the steps to reset your Vevor heat press:
- Turn off the heat press and unplug it from the power source.
- Wait for about 10 minutes to allow the machine to cool down.
- Plug the heat press back in and turn it on.
- Set the temperature and time settings to your desired values.
- Run a test press to ensure the machine is working correctly.
If resetting the machine does not solve the issue, it might need professional repair. Always refer to the user manual for specific troubleshooting steps and safety tips.
Issue | Possible Solution |
---|---|
Display Not Working | Check power source, inspect cord, test outlet |
Error Messages | Inspect display panel, replace control board |
Machine Not Resetting | Follow reset steps, contact support if unresolved |
Remember, regular maintenance can prevent many issues. Keep your Vevor heat press clean and inspect it regularly. This helps ensure your machine works efficiently and lasts longer.
Manual Vs. Automatic Press: Unique Challenges
Choosing between a manual and automatic heat press can be difficult. Each type has its own unique challenges that users must navigate. Understanding these challenges helps in making a more informed decision. This section explores the quirks of manual presses and optimizes automatic press performance.
Handling Manual Press Quirks
Manual presses require user intervention for each step. This means you control the pressure, temperature, and timing. Here are some common issues and their solutions:
- Uneven Pressure: Ensure the press is on a flat surface. Check for any obstructions under the platen.
- Temperature Fluctuations: Use an infrared thermometer to verify temperature. Adjust settings accordingly.
- Inconsistent Timing: Use a timer to ensure consistent application times. Set alarms if needed.
Regular maintenance is crucial for manual presses. Lubricate moving parts to prevent wear and tear. Always follow the manufacturer’s guidelines.
Optimizing Automatic Press Performance
Automatic presses offer convenience but come with their own challenges. These machines rely on software and sensors for operation. Here are some tips to optimize performance:
- Software Updates: Regularly update the software. This ensures optimal performance and fixes bugs.
- Sensor Calibration: Periodically calibrate sensors to maintain accuracy. Follow the manufacturer’s calibration guide.
- Electrical Issues: Check for loose wires and connections. Ensure the machine is properly grounded.
Automatic presses also benefit from regular maintenance. Clean the sensors and check the software for updates. This keeps the machine running smoothly.
Issue | Manual Press | Automatic Press |
---|---|---|
Pressure Control | User-controlled | Sensor-controlled |
Temperature Stability | Manual adjustment | Automatic regulation |
Timing Consistency | User-reliant | Programmed |
Understanding these unique challenges helps in effective troubleshooting. Whether using a manual or automatic press, proper maintenance ensures longevity and optimal performance.
When To Seek Professional Help
Encountering problems with your Vevor Heat Press can be frustrating. Some issues are simple to fix, but others require expert intervention. Knowing when to seek professional help can save time and prevent further damage.
Recognizing Complex Issues
Some problems are too complex for DIY solutions. Burnt prints or erratic temperature readings often need professional help. If the machine won’t turn on despite checking the power supply, it’s time to call an expert.
Issue | Description |
---|---|
Inconsistent Heating | Heat varies across the platen. |
Electrical Smell | Burnt smell indicating a possible short circuit. |
Unresponsive Controls | Buttons or touchpad not working. |
Finding Qualified Technicians
Finding a qualified technician is crucial. Look for technicians with experience in heat press machines. Check reviews and ratings to gauge their reliability.
- Ask for certifications or training in heat press repair.
- Ensure they provide a warranty on their repairs.
- Request a detailed quote before agreeing to services.
Professional help ensures your heat press functions efficiently. It can extend the lifespan of your machine and improve the quality of your prints.
Leveraging Warranties And Customer Support
Troubleshooting a Vevor Heat Press can be daunting. Leveraging warranties and customer support can ease the process. Understanding your coverage and navigating support channels are essential for resolving issues efficiently.
Understanding Your Coverage
Your Vevor Heat Press comes with a warranty. This warranty covers specific defects and malfunctions. Knowing what your warranty covers helps you make informed decisions.
Refer to the user manual for detailed warranty information. The manual lists the components and issues covered under warranty. Keep a copy of your receipt. This receipt is essential for warranty claims.
Component | Warranty Period |
---|---|
Heating Element | 1 Year |
Control Panel | 6 Months |
Frame | 2 Years |
If your issue is covered, contact customer support. They will guide you through the next steps. Remember, using the heat press incorrectly might void the warranty. Always follow the manufacturer’s instructions.
Navigating Support Channels
Vevor offers multiple support channels. These include phone, email, and online chat. Choose the one that suits you best.
- Phone Support: Call the support number listed in your manual.
- Email Support: Send an email with a detailed description of your issue.
- Online Chat: Use the chat feature on the Vevor website for quick assistance.
Prepare the following information before contacting support:
- Model number of your heat press.
- Details of the issue you are facing.
- Steps you have already taken to resolve it.
- Proof of purchase.
Customer support may ask you to perform troubleshooting steps. Follow these steps carefully and report the results. This helps in diagnosing the problem accurately.
For complex issues, they might suggest sending the unit for repair. If the issue falls under warranty, repairs might be free. If not, they will provide a cost estimate.
Enhancing Longevity And Performance
Keeping your Vevor Heat Press in top shape ensures its longevity and peak performance. This guide will help you with daily use and upgrading parts to improve functionality.
Best Practices For Daily Use
Following best practices daily can significantly enhance your heat press’s lifespan. Here are some key tips:
- Preheat the Press: Always preheat before use to ensure even temperature distribution.
- Clean the Surface: Wipe the platen surface after each use to remove residues.
- Check Pressure Settings: Adjust the pressure settings according to the material.
- Turn Off After Use: Always turn off the machine when not in use to prevent overheating.
Upgrading Parts For Improved Functionality
Upgrading parts can greatly enhance your heat press’s performance. Here are some parts you may consider upgrading:
Part | Upgrade Benefit |
---|---|
Platen | Improves heat distribution and reduces cold spots. |
Heat Pads | Provides better insulation and consistent pressure. |
Temperature Controller | Ensures accurate temperature settings for varied materials. |
Regular maintenance and timely upgrades can keep your Vevor Heat Press running smoothly for years. Implement these tips to enjoy seamless and efficient operation.
Frequently Asked Questions
Why Is My Vevor Heat Press Not Heating?
Check the power connection and ensure the temperature settings are correct. A faulty heating element might also be the issue.
How Do I Reset My Vevor Heat Press?
Unplug the machine for a few minutes, then plug it back in. This should reset the heat press.
What If My Vevor Heat Press Shows An Error Code?
Refer to the user manual for specific error codes. Common issues include sensor faults or power supply problems.
Why Is My Heat Press Not Pressing Evenly?
Ensure the pressure is set correctly. The silicone pad might need replacing if it’s worn out.
How Do I Clean My Vevor Heat Press?
Turn off and unplug the machine. Use a soft cloth with mild detergent to clean the surface carefully.
Conclusion
Mastering Vevor heat press troubleshooting ensures smooth, efficient operations. Follow our guide to tackle common issues easily. Regular maintenance and timely fixes enhance your press’s longevity. Stay proactive, and your heat press will deliver optimal results for years. Happy pressing!