Pitco fryer troubleshooting involves identifying error codes and checking common issues like power supply and thermostat settings. Regular maintenance helps prevent problems.
Pitco fryers are essential in commercial kitchens, ensuring quick and efficient frying. However, even the best equipment can encounter issues. Understanding common problems and their solutions can save time and reduce downtime. Start by checking the power supply, thermostat settings, and error codes displayed on the fryer.
Cleaning and regular maintenance also play crucial roles in keeping the fryer in optimal condition. By addressing these aspects, you can ensure the longevity and efficiency of your Pitco fryer, keeping your kitchen running smoothly.
Identifying Common Pitco Fryer Issues
Contents
- 1 Identifying Common Pitco Fryer Issues
- 2 Starting With The Basics: Power And Connectivity
- 3 Temperature Challenges In Pitco Fryers
- 4 Oil Filtration And Quality Maintenance
- 5 Pilot Light And Ignition Solutions
- 6 Dealing With Unusual Noises And Odors
- 7 Component-specific Issues: Burners, Baskets, And More
- 8 Advanced Pitco Fryer Troubleshooting
- 9 Preventative Measures And Best Practices
- 10 Frequently Asked Questions
- 11 Conclusion
Ensuring your Pitco fryer functions well is crucial. Knowing common problems can save time and money. This guide helps you understand common issues and how to fix them.
Symptoms Of Malfunction
Recognizing the symptoms of a malfunctioning Pitco fryer is essential. Here are some common signs:
- Inconsistent Temperature: The oil heats up unevenly.
- Strange Noises: Unusual sounds like popping or hissing.
- Burnt Food: Food cooks too quickly or unevenly.
- Oil Leaks: Oil drips from unexpected places.
- Slow Recovery Time: Oil takes longer to heat up again.
Frequent Error Codes And Their Meanings
Error codes help diagnose problems in your Pitco fryer. Here are some frequent error codes and what they mean:
Error Code | Meaning |
---|---|
E10 | High Limit Sensor Failure |
E20 | Temperature Probe Failure |
E41 | Ignition Failure |
E46 | Oil Level Sensor Failure |
E47 | Filter Pump Failure |
Starting With The Basics: Power And Connectivity
Troubleshooting a Pitco fryer can seem daunting. Starting with the basics helps. Ensuring power and connectivity are crucial first steps. Without proper power, your fryer won’t function. Gas connections are equally important. Below, find steps to ensure everything is connected correctly.
Ensuring Proper Electrical Supply
Verify the fryer is plugged into a working outlet. Check the outlet with another device. Inspect the power cord for any damage. Replace if you find cuts or frays. Ensure the circuit breaker hasn’t tripped. Reset it if needed.
Step | Action |
---|---|
1 | Plug fryer into a working outlet |
2 | Check the outlet with another device |
3 | Inspect power cord for damage |
4 | Replace damaged power cord |
5 | Reset circuit breaker if tripped |
Checking Gas Connections And Pressure
Ensure the gas supply valve is open. Check connections for leaks using soapy water. Bubbles indicate a leak. Tighten connections if needed. Ensure the gas pressure matches the fryer’s specifications. Use a manometer to measure pressure. Adjust regulator if pressure is too high or low.
- Open gas supply valve
- Check connections with soapy water
- Tighten connections if bubbles appear
- Measure gas pressure with a manometer
- Adjust regulator to correct pressure
Temperature Challenges In Pitco Fryers
Maintaining the right temperature in your Pitco fryer is crucial. Temperature issues can affect food quality and safety. Understanding these challenges helps keep your fryer running smoothly.
Calibrating Thermostats
Thermostat calibration ensures your fryer heats to the correct temperature. An inaccurate thermostat can lead to cooking problems. To calibrate:
- Turn off the fryer and let it cool.
- Locate the thermostat knob and remove it.
- Use a calibration tool to adjust the settings.
- Turn the fryer back on and test the temperature.
Repeat these steps until the thermostat is accurate. Always use a reliable thermometer for testing.
Dealing With Overheating Or Underheating
Overheating or underheating can spoil your food. Here are some tips to address these issues:
Issue | Potential Cause | Solution |
---|---|---|
Overheating | Faulty thermostat | Replace or recalibrate the thermostat. |
Underheating | Clogged burners | Clean the burners thoroughly. |
Inconsistent heating | Electrical issues | Check wiring and connections. |
Regular maintenance reduces the risk of temperature issues. Clean your fryer and check the thermostat often.
Oil Filtration And Quality Maintenance
Maintaining the quality of oil in your Pitco fryer is crucial. Proper oil filtration ensures food tastes great and the fryer works well. Follow these steps to keep your fryer in top condition.
Routine Cleaning Steps
Regular cleaning is essential to maintain your fryer’s performance and extend its lifespan.
- Turn off the fryer and let the oil cool.
- Drain the oil into a container.
- Remove and clean the fryer basket.
- Wipe the inside of the fryer with a clean cloth.
- Wash all parts with warm soapy water.
- Rinse and dry thoroughly.
- Refill the fryer with filtered oil.
Troubleshooting Filtration System Glitches
Sometimes, the filtration system may face issues. Here are some common problems and solutions.
Issue | Possible Cause | Solution |
---|---|---|
Oil not filtering | Clogged filter | Clean or replace the filter |
Slow filtration | Low pump pressure | Check and adjust the pump |
Oil leakage | Loose connections | Tighten all fittings |
By following these troubleshooting steps, you can ensure your Pitco fryer runs smoothly.
Pilot Light And Ignition Solutions
Pitco fryers are reliable, but pilot light and ignition issues can occur. Solving these problems ensures your fryer operates smoothly. In this section, we’ll cover solutions for these common issues.
Relighting The Pilot
If the pilot light goes out, follow these steps to relight it:
- Turn the gas valve to the “off” position.
- Wait five minutes to clear any gas buildup.
- Turn the gas valve to the “pilot” position.
- Hold down the pilot button and use a lighter to ignite it.
- Continue holding the button for 30 seconds, then release.
- Turn the valve to the “on” position.
Addressing Ignition Failures
If the pilot light fails to ignite, check these potential issues:
- Gas Supply: Ensure the gas supply is turned on.
- Thermocouple: Inspect if it’s clean and properly aligned.
- Pilot Orifice: Clear any blockages in the pilot orifice.
- Ignition Module: Verify if the ignition module functions correctly.
If problems persist, consult the Pitco fryer manual or contact a technician. Proper maintenance will keep your fryer running efficiently.
Dealing With Unusual Noises And Odors
Experiencing unusual noises and odors from your Pitco fryer can be alarming. These issues often signal underlying problems. Addressing them promptly ensures your fryer operates efficiently and safely. Below, we explore common sources and remedies for these disturbances.
Identifying The Source Of The Sound
Strange sounds from your Pitco fryer can indicate various issues. Follow these steps to identify the source:
- Hissing sounds might come from oil overheating. Check the thermostat.
- Banging noises could suggest loose components. Inspect and tighten any loose parts.
- Grinding sounds often point to motor issues. Examine the motor for wear and tear.
If the noise persists, refer to the user manual or consult a technician. Proper diagnosis is crucial for a lasting fix.
Remedies For Unpleasant Smells
Foul odors from your Pitco fryer can stem from several causes. Use the following methods to eliminate these smells:
Cause | Remedy |
---|---|
Old oil | Replace the oil and clean the fryer. |
Food residue | Remove and clean the basket and interior surfaces. |
Burnt particles | Filter the oil regularly to remove debris. |
Maintaining a regular cleaning schedule can prevent unpleasant odors. Always ensure the fryer is cooled down before cleaning.
By identifying and addressing these issues, you can maintain your fryer’s performance. This not only prolongs its life but also ensures safe and efficient operation.
Component-specific Issues: Burners, Baskets, And More
Dealing with a Pitco fryer can sometimes be tricky. Understanding issues with specific components helps. Let’s dive into common problems with burners and baskets.
Cleaning And Maintenance Of Burners
The burners are the heart of your Pitco fryer. Keeping them clean ensures efficiency. Regular cleaning can prevent many issues.
- Turn off the fryer and let it cool.
- Remove the burners carefully.
- Use a soft brush to clean the burners.
- Check for any blockages or debris.
- Reassemble the burners properly.
Perform this task weekly. It helps maintain the fryer’s performance.
Basket Problems And How To Fix Them
Baskets are essential for cooking. Problems with them can disrupt your workflow. Here are common issues and fixes:
- Broken Handles: Replace the handle immediately.
- Warped Basket: Replace the basket for even cooking.
- Stuck Food: Soak in warm water and scrub gently.
Regular checks can help identify these problems early. Always use baskets that fit your fryer model.
Maintaining these components ensures your Pitco fryer works efficiently. Keep an eye on these parts and perform regular checks.
Advanced Pitco Fryer Troubleshooting
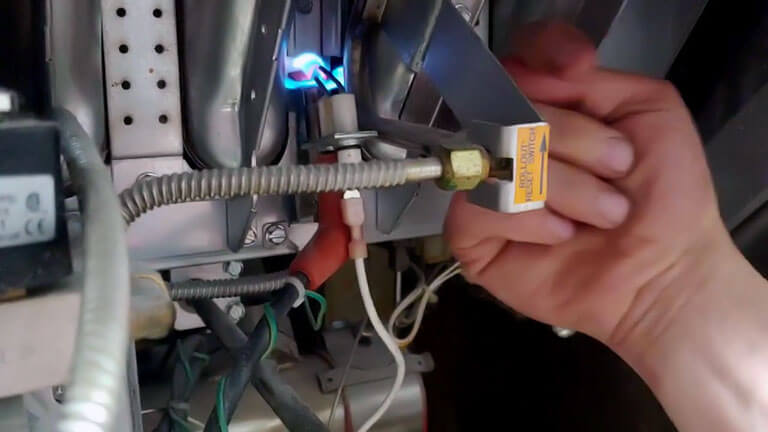
Advanced Pitco Fryer Troubleshooting requires detailed knowledge and skill. This section will guide you through complex issues. It will also help you understand when to call a professional and warranty options.
When To Call A Professional
Some issues need expert attention. Calling a professional is best in these cases:
- Electrical problems
- Gas leaks
- Burner malfunctions
- Control panel errors
Experts have the right tools and skills. They can fix these issues safely and quickly. Trying to fix them yourself can be dangerous and costly.
Understanding Warranty And Service Options
Knowing your warranty and service options is crucial. Here’s a table to help you:
Issue | Covered by Warranty | Service Option |
---|---|---|
Electrical faults | Yes | Call the manufacturer |
Gas leaks | Yes | Call the manufacturer |
Control panel errors | Yes | Call the manufacturer |
General maintenance | No | Hire a service technician |
Always check your warranty details. It can save you money and time. For out-of-warranty issues, find a trusted service technician.
Preventative Measures And Best Practices
Ensuring the longevity and efficiency of your Pitco fryer involves taking key preventative measures and adhering to best practices. Proper maintenance and staff training can minimize downtime and extend the life of your equipment. Below, we outline essential steps to keep your Pitco fryer operating at peak performance.
Regular Maintenance Schedule
Establishing a regular maintenance schedule is vital for your Pitco fryer. Consistent checks and cleanings can prevent major issues and ensure optimal performance.
- Daily Cleaning: Wipe down the fryer exterior and clean the oil.
- Weekly Tasks: Inspect and clean the burners, and check the pilot light.
- Monthly Maintenance: Examine and clean the filter system.
- Quarterly Check: Inspect and replace worn-out parts.
Maintaining this schedule helps to avoid unexpected breakdowns and costly repairs.
Training Staff For Efficient Operation
Proper staff training is crucial for the efficient operation of your Pitco fryer. Well-trained employees can identify and address minor issues before they escalate.
- Basic Operation: Teach staff how to operate the fryer correctly.
- Safety Protocols: Ensure they understand and follow safety procedures.
- Troubleshooting Skills: Train them to recognize common issues and perform basic fixes.
- Cleaning Routines: Educate them on daily and weekly cleaning tasks.
Investing in staff training reduces the risk of operational errors and enhances the fryer’s lifespan.
Incorporating these preventative measures and best practices into your routine can significantly improve your Pitco fryer’s performance and durability. By maintaining a regular schedule and training your staff efficiently, you ensure a smooth, trouble-free operation.
Frequently Asked Questions
Why Is My Pitco Fryer Not Heating?
Check the thermostat and heating element. These components often cause heating issues.
How To Reset Pitco Fryer?
Locate the reset button near the thermostat. Press it to reset your fryer.
Why Is My Pitco Fryer Beeping?
Your fryer might be signaling an error. Check the display for error codes.
How To Fix Pitco Fryer Error Codes?
Consult the user manual. Error codes indicate specific issues needing attention.
Why Does My Pitco Fryer Keep Shutting Off?
Overheating or a faulty thermostat could cause this. Inspect and replace as needed.
Conclusion
Mastering Pitco fryer troubleshooting can save time and money. Regular maintenance keeps your fryer running smoothly. Address issues promptly to ensure delicious, consistent results. With these tips, you’ll maintain peak performance and extend your fryer’s lifespan. Keep this guide handy for quick reference and enjoy hassle-free frying.