To troubleshoot a Porter Cable air compressor, check the power source and inspect the pressure switch. Ensure all connections are secure and intact.
Porter Cable air compressors are reliable tools for various tasks, from inflating tires to powering pneumatic tools. Despite their durability, issues can arise that hinder performance. Addressing these problems promptly is crucial to maintain efficiency and prolong the compressor’s life.
Key troubleshooting steps include examining the power supply, inspecting the pressure switch, and checking for any leaks or unusual noises. Regular maintenance and timely repairs ensure the compressor remains in optimal working condition. This guide will help you diagnose and fix common problems, ensuring your Porter Cable air compressor operates smoothly.
Introduction To Porter Cable Air Compressors
Porter Cable air compressors are reliable and powerful. They are used for various tasks. These compressors are popular due to their efficiency and durability. They offer excellent performance for both home and professional use.
The Popularity Of Porter Cable Compressors
Porter Cable compressors are known for their quality. They are trusted by many professionals. Their popularity comes from their robust design and long-lasting performance. Users appreciate the brand for its consistent output and minimal maintenance.
Many people prefer Porter Cable compressors due to their ease of use. Even beginners find them user-friendly. The compressors come with clear instructions and safety features. This makes them a top choice for many users.
Porter Cable compressors are available in various models. Each model meets different needs. This variety makes it easy to find the right compressor for any task. Whether you need a small unit or a powerful one, Porter Cable has options.
Common Usage Scenarios
Porter Cable compressors are used in many scenarios. They are helpful in home improvement projects. For example, they can power nail guns and paint sprayers.
Professionals use these compressors in workshops. They are ideal for running air tools like impact wrenches. The compressors provide consistent air pressure, making tasks easier.
Porter Cable compressors are also used in automotive repair. They help in inflating tires and operating pneumatic tools. The compressors are portable, which makes them convenient to move around.
Even hobbyists find these compressors useful. They can power airbrushes for painting models. The versatility of Porter Cable compressors makes them a valuable tool.
Identifying Common Issues
Porter Cable air compressors are reliable and efficient. Yet, they can face issues. Identifying common problems helps maintain their longevity and performance. This section highlights frequent issues and how to address them.
Pressure Irregularities
Pressure problems are common with air compressors. If the pressure is too low or too high, it can affect your work. Ensure the pressure gauge is working correctly. Check for blockages in the air hose. Inspect the pressure switch for damage. A faulty switch can cause irregular pressure.
Possible Cause | Solution |
---|---|
Blocked air hose | Clean or replace the hose |
Faulty pressure gauge | Replace the gauge |
Damaged pressure switch | Replace the switch |
Motor Problems
A malfunctioning motor can stop your air compressor. Check if the power supply is consistent. Inspect the motor capacitor for faults. A bad capacitor can prevent the motor from starting. Ensure the motor overload protector is not tripped. If it is, reset it.
- Ensure power supply is stable
- Check motor capacitor
- Reset motor overload protector
Leakages And Airflow Obstructions
Leaks and obstructions affect your compressor’s efficiency. Examine the air fittings for leaks. Tighten or replace them if needed. Check for debris in the air filter. Clean or replace the filter regularly. Inspect the drain valve for proper function. A faulty drain valve can cause leaks.
- Check air fittings for leaks
- Clean or replace air filter
- Inspect and replace faulty drain valve
Quick Diagnostic Steps
Is your Porter Cable Air Compressor acting up? Don’t worry! Follow these quick diagnostic steps to identify and fix common issues. This guide will help you get your compressor back in action in no time.
Safety Precautions
Before starting any troubleshooting, follow these safety precautions:
- Turn off the air compressor.
- Unplug the unit from the power source.
- Release any built-up air pressure.
- Wear protective gloves and safety glasses.
Safety is crucial. Ensure the unit is off and unplugged.
Initial Assessment
Perform an initial assessment to identify obvious issues:
- Check for visible damage or leaks.
- Listen for unusual noises or vibrations.
- Ensure the power cord is in good condition.
- Inspect the air filters and clean if dirty.
Look closely for any signs of wear or damage. This helps in identifying the problem quickly.
Tools Needed For Troubleshooting
Gather the following tools for a thorough troubleshooting:
Tool | Purpose |
---|---|
Multimeter | Check electrical continuity |
Wrenches | Tighten or loosen bolts and nuts |
Screwdrivers | Remove or tighten screws |
Air Pressure Gauge | Measure air pressure levels |
Soapy Water | Detect air leaks |
Having these tools will make the troubleshooting process easier.
Resolving Pressure Fluctuations
Pressure fluctuations in your Porter Cable air compressor can be frustrating. Understanding how to resolve these issues ensures smooth operation and extends the life of your unit.
Checking The Pressure Regulator
The pressure regulator controls the air pressure output. If the pressure fluctuates, first check the regulator. Ensure it is set correctly and not damaged.
- Turn off the compressor.
- Inspect the regulator for any signs of wear or damage.
- Adjust the regulator to the desired pressure setting.
Adjusting Cut-in And Cut-out Settings
The cut-in and cut-out settings manage when the compressor starts and stops. Incorrect settings can cause pressure fluctuations. Adjust these settings to maintain consistent pressure.
- Turn off the compressor.
- Locate the adjustment screws for cut-in and cut-out settings.
- Use a screwdriver to adjust the cut-in setting to the desired start pressure.
- Adjust the cut-out setting to the desired stop pressure.
- Turn on the compressor and monitor the pressure gauge.
Setting | Recommended Pressure (PSI) |
---|---|
Cut-In | 90 PSI |
Cut-Out | 120 PSI |
Fixing Motor Malfunctions
Porter Cable air compressors are sturdy, but motor malfunctions can arise. This section will guide you through fixing common motor issues.
Resetting The Overload Switch
The overload switch can trip due to excessive use. Resetting it can often solve motor issues.
- Turn off the air compressor and unplug it.
- Locate the overload switch. It is usually near the motor.
- Press the reset button. Hold it for a few seconds.
- Plug in the air compressor and turn it on.
If the motor runs smoothly, the issue was likely an overloaded switch.
Capacitor Testing And Replacement
A faulty capacitor can hinder motor performance. Test and replace it if needed.
- Turn off and unplug the air compressor.
- Locate the motor capacitor. It is often cylindrical.
- Discharge the capacitor using a resistor.
- Use a multimeter to test the capacitor.
Reading | Action |
---|---|
Within Range | The capacitor is fine. |
Out of Range | Replace the capacitor. |
- Install a new capacitor if the old one is faulty.
- Reconnect all wires and secure the capacitor.
- Plug in and start the air compressor.
A working capacitor ensures optimal motor performance.
Addressing Leakages
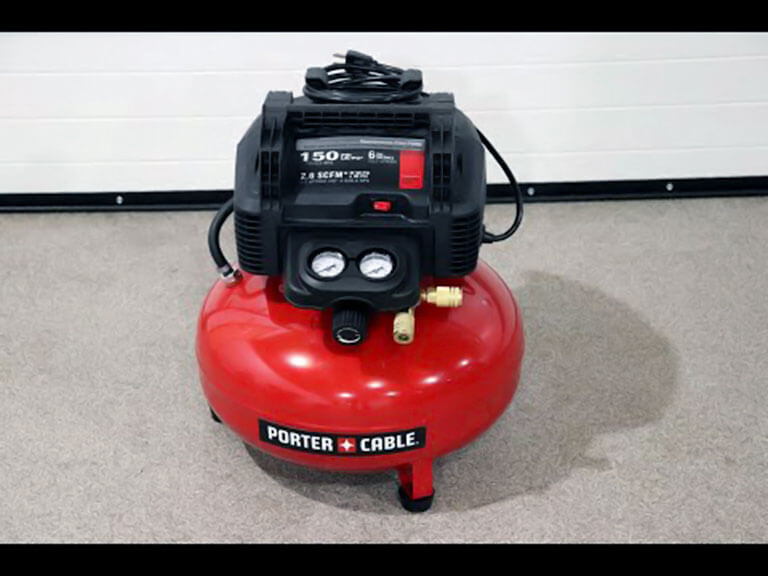
Leakages in a Porter Cable air compressor can reduce its efficiency. Detecting and fixing these leaks is crucial. This guide will help you address leakages in your air compressor.
Detecting Air Leaks
To detect air leaks, start by turning off the air compressor. Ensure it is fully charged. Listen for any hissing sounds. These sounds can help you find leaks.
You can also use a soapy water solution. Mix soap and water in a spray bottle. Spray the solution on the compressor’s connections and hoses. Bubbles will form where there are leaks.
Sealing And Repair Techniques
Once you identify the leaks, it’s time to seal them. For small leaks, use Teflon tape. Wrap the tape around the threads of the leaking connection.
For larger leaks, you might need to replace parts. This includes hoses, valves, or fittings. Always ensure the replacement parts are compatible with your air compressor model.
You can also use a pipe sealant for persistent leaks. Apply the sealant to the threads of the connections. Allow it to dry before using the compressor again.
Leak Source | Repair Method |
---|---|
Hose | Replace hose |
Connections | Wrap with Teflon tape |
Valves | Replace valve |
Fittings | Apply pipe sealant |
Make sure to test the compressor after repairs. Ensure no further leaks are present. Regular maintenance helps prevent future leaks. Check all parts periodically.
Unclogging Air Filters And Hoses
Porter Cable air compressors are reliable tools. But clogged air filters and hoses can hinder performance. Learn how to clean and inspect these components. This ensures your compressor works efficiently.
Cleaning Air Filters
Air filters keep dust and debris out. A dirty filter can reduce airflow. Follow these steps to clean your air filter:
- Turn off and unplug the compressor.
- Locate the air filter housing.
- Remove the filter carefully.
- Use a soft brush to remove dust.
- Rinse the filter with water if needed.
- Let it dry completely before reinstalling.
Replace the filter if it is damaged. A clean filter ensures better airflow and efficiency.
Inspecting And Replacing Hoses
Hoses can get clogged or damaged. Regular inspection helps avoid performance issues. Here’s how to inspect and replace hoses:
- Turn off and unplug the compressor.
- Detach the hoses from the compressor.
- Check for visible clogs or damage.
- Run water through the hose to clear minor clogs.
- Replace the hose if you find cracks or holes.
Use the correct hose type for your compressor. This ensures safety and efficiency.
Regular Maintenance Tips
Keeping your Porter Cable air compressor in top condition requires regular maintenance. Follow these simple tips to ensure your compressor runs smoothly and lasts longer. This guide will cover Lubrication Guidelines and Storage Recommendations.
Lubrication Guidelines
Proper lubrication is key to maintaining your air compressor. Here are some essential steps:
- Check the oil level regularly. Add oil if needed.
- Use only the recommended oil type for your compressor model.
- Change the oil every 500 hours of operation or every six months.
Neglecting lubrication can cause severe damage. Always keep an eye on the oil level and quality.
Storage Recommendations
Storing your air compressor correctly can extend its lifespan. Follow these tips:
- Keep the compressor in a cool, dry place.
- Drain the tank to prevent moisture buildup.
- Cover the compressor to protect it from dust and debris.
- Store hoses and accessories in a clean, dry area.
Proper storage can prevent rust and other issues, ensuring your compressor is ready for use.
By following these regular maintenance tips, you can keep your Porter Cable air compressor in excellent condition. Regular checks and proper storage are crucial for long-term performance.
When To Seek Professional Help
Porter Cable air compressors are reliable, but sometimes issues arise. Knowing when to seek professional help can save time and money. Here, we’ll guide you through assessing the severity of issues and finding qualified technicians.
Assessing The Severity Of Issues
Some problems can be fixed with basic troubleshooting. However, certain signs indicate it’s time to consult a professional. Look out for the following:
- Unusual noises: Grinding, hissing, or banging sounds.
- Power issues: Compressor won’t start or frequently trips breakers.
- Inconsistent pressure: Pressure drops or fluctuates excessively.
- Leaks: Visible air or oil leaks.
If you notice any of these signs, professional help might be necessary. Continuing to use the compressor with these issues can lead to further damage.
Finding Qualified Technicians
Finding the right technician is crucial. Here are steps to ensure you select a qualified professional:
- Research: Look for certified and experienced technicians online.
- Check reviews: Read customer reviews and ratings.
- Ask for recommendations: Seek advice from friends or family.
- Verify credentials: Ensure the technician has proper certification and training.
- Compare costs: Get quotes from multiple technicians to ensure fair pricing.
Using these steps will help you find a reliable technician to fix your Porter Cable air compressor.
Issue | Professional Needed? |
---|---|
Unusual noises | Yes |
Power issues | Yes |
Inconsistent pressure | Yes |
Leaks | Yes |
By assessing the severity of issues and finding qualified technicians, you can keep your Porter Cable air compressor running smoothly.
Frequently Asked Questions
How Do I Reset My Porter Cable Air Compressor?
To reset, turn off the compressor, unplug it, and wait for 15 minutes. Plug back in and restart.
Why Is My Porter Cable Air Compressor Not Building Pressure?
Check for leaks in hoses and connections. Inspect the intake filter and ensure the tank drain valve is closed.
What Causes My Air Compressor To Overheat?
Overheating can occur due to poor ventilation or extended use. Ensure proper airflow and allow time for cooling.
How Do I Fix A Leaking Air Compressor?
Tighten any loose connections and replace damaged hoses or seals. Check for pinhole leaks in the tank.
Why Won’t My Air Compressor Start?
Check the power source, and ensure the switch is on. Inspect the fuse or circuit breaker for issues.
Conclusion
Fixing your Porter Cable air compressor is now easier with these troubleshooting tips. Regular maintenance ensures optimal performance. Address issues promptly to prolong the compressor’s lifespan. Keep this guide handy for quick reference. Enjoy efficient air compression and smooth operation for all your projects.
Thank you for reading and happy repairing!