Ensure the water supply is on and the flush valve is free of debris. Replace faulty parts if necessary.
Sloan flush valves are essential for maintaining efficient and sanitary restroom facilities. They are widely used in commercial settings due to their durability and reliability. Proper troubleshooting can prevent common issues like leaks, weak flushes, and continuous running. Understanding the basic components and their functions helps in diagnosing problems quickly.
Regular maintenance and timely repairs ensure the longevity and efficiency of the flush valves. Following a systematic approach to troubleshooting can save time and reduce maintenance costs. This guide provides practical steps to identify and resolve common issues with Sloan flush valves, ensuring optimal performance and user satisfaction.
Introduction To Sloan Flush Valves
Sloan Flush Valves are essential in modern restrooms. These valves help control water flow efficiently. They are mostly found in commercial buildings. Proper maintenance of these valves is crucial.
Understanding their functionality helps in quick troubleshooting. This guide will assist you in identifying common issues and their solutions.
Common Issues With Flush Valves
- Continuous Running: Water keeps flowing without stopping.
- Weak Flush: The flush lacks power to clear the bowl.
- Handle Sticking: The handle doesn’t return to its position.
- Leaking at Handle: Water leaks from the handle area.
Benefits Of Quick Troubleshooting
Quick troubleshooting of Sloan Flush Valves offers many benefits.
- Water Conservation: Fixing issues saves water.
- Cost Savings: It reduces water bills.
- Improved Hygiene: Proper flushing ensures cleanliness.
- Extended Valve Life: Regular maintenance prolongs valve lifespan.
Addressing these issues promptly is important. It ensures the smooth operation of restrooms. This keeps users satisfied and prevents costly repairs.
Identifying Your Sloan Valve Model
Identifying your Sloan flush valve model is the first step in troubleshooting. Knowing the model helps in finding the right parts and instructions. This guide will help you locate the model number and explain why it’s important.
Locating The Model Number
Finding the model number is easy if you know where to look. Below are some common places to find it:
- Valve Body: Check the valve body for a stamped or printed number.
- Flush Handle: Sometimes, the model number is near the flush handle.
- Instruction Manual: The manual often lists the model number.
If you still can’t find it, check the manufacturer’s website for guidance.
Why Model Identification Matters
Model identification is crucial for several reasons:
- Correct Parts: Ensures you get the right replacement parts.
- Accurate Instructions: Follow instructions specific to your model.
- Warranty Claims: Needed for any warranty claims or services.
Identifying your model saves time and avoids frustration. It helps you fix issues quickly and correctly.
Initial Diagnostic Steps
When troubleshooting a Sloan flush valve, start with the initial diagnostic steps. This helps identify the root cause quickly. Follow these steps to ensure proper functioning.
Observing Flush Valve Behavior
Observe the flush valve behavior closely. Notice any irregularities. Watch for common issues like:
- Continuous flushing
- Weak flush
- No flush
- Water leaks
These symptoms provide clues about potential issues. Take note of each problem observed.
Quick Inspection Checklist
Use this quick inspection checklist to diagnose Sloan flush valve issues:
Inspection Point | Action |
---|---|
Supply Line | Check for blockages or leaks. |
Handle | Ensure it moves freely. |
Diaphragm | Inspect for wear and tear. |
Vacuum Breaker | Check for proper installation. |
Flush Volume | Verify correct adjustment. |
Go through each checklist item. Address any issues found. This can solve many common problems.
Solving Flush Inconsistencies
Experiencing flush inconsistencies with your Sloan Flush Valve? It’s frustrating. An inconsistent flush can waste water and cause inconvenience. This guide helps you identify and solve flush inconsistencies. Follow these steps to get your flush valve working perfectly.
Adjusting Flush Volume
To adjust the flush volume, locate the adjustment screw. This screw is usually found on the valve body. Follow these steps:
- Turn off the water supply.
- Remove the valve cover.
- Locate the adjustment screw.
- Turn the screw clockwise to increase flush volume.
- Turn the screw counterclockwise to decrease flush volume.
- Replace the valve cover.
- Turn on the water supply.
Check the flush after adjusting. Repeat if necessary. Proper flush volume ensures efficient water use.
Dealing With Phantom Flushes
Phantom flushes happen when the toilet flushes by itself. This can be caused by:
- A worn-out diaphragm.
- A damaged relief valve.
- A faulty handle assembly.
Follow these steps to fix phantom flushes:
- Turn off the water supply.
- Remove the valve cover.
- Inspect the diaphragm and relief valve.
- Replace any worn-out or damaged parts.
- Check the handle assembly for wear.
- Replace the handle assembly if needed.
- Replace the valve cover.
- Turn on the water supply.
Phantom flushes waste water and can be annoying. Fixing them saves water and peace of mind.
Handling Water Leaks And Drips
Water leaks and drips in Sloan flush valves can be annoying. They can lead to water waste and higher bills. Knowing how to handle these issues can save you time and money. Here’s how to troubleshoot and fix water leaks and drips in your Sloan flush valve.
Seal And Gasket Checks
Start by checking the seals and gaskets. These parts often cause leaks. Look for any visible wear or damage. If they appear cracked or broken, they need replacement.
Use a flashlight to inspect the inside of the valve. Ensure all seals are intact and properly seated. A simple adjustment might fix the leak. If not, replacement is necessary.
Step | Action |
---|---|
1 | Turn off the water supply. |
2 | Remove the flush valve cover. |
3 | Inspect seals and gaskets for damage. |
4 | Replace damaged parts. |
When To Replace Components
Sometimes, seals and gaskets are not the only problem. Other components might need replacement. If leaks persist, consider replacing the diaphragm kit. This kit includes many parts that can wear out over time.
Use this simple checklist:
- Diaphragm kit
- Handle assembly
- Flush valve cover
Replacing these parts is straightforward:
- Turn off the water supply.
- Remove the old components.
- Install new parts from the kit.
- Turn on the water supply and test the valve.
Always use genuine Sloan parts. They ensure compatibility and longevity. Regular maintenance can prevent future leaks and drips.
Unclogging A Sloan Valve
Unclogging a Sloan valve is essential for maintaining your restroom facilities. Clogs can cause water flow issues and decrease efficiency. This guide will help you address common clogging issues and keep your Sloan valve in top condition.
Clearing Debris From The Valve
Debris can cause significant clogging in your Sloan valve. Regular cleaning is crucial.
- Turn off the water supply: This is the first step to avoid flooding.
- Remove the valve cover: Use a wrench to unscrew the cover.
- Inspect the diaphragm: Check for any visible debris or damage.
- Clean the diaphragm: Use a soft brush to remove any debris.
- Reassemble the valve: Ensure all parts are secured properly.
- Turn the water supply back on: Test for proper water flow.
Regular maintenance can prevent major issues. Always check the valve components for wear and tear.
Preventive Measures For Clogs
Preventing clogs is more effective than dealing with them later. Follow these tips:
- Install water filters: Water filters can trap debris before it reaches the valve.
- Schedule regular inspections: Inspect the valve components every few months.
- Use high-quality water: Ensure your water supply is clean and free from impurities.
- Educate users: Inform users about proper restroom use to avoid foreign objects in the system.
Implementing these measures can extend the life of your Sloan valve. Proper care ensures smooth operation and reduces maintenance costs.
Fixing Handle Problems
Having problems with your Sloan flush valve handle can be frustrating. This guide will help you troubleshoot common handle issues. Follow these steps to get your flush valve working smoothly again.
Loose Or Sticking Handles
A loose or sticking handle can cause the flush valve to malfunction. Here’s how to fix these issues:
- Check for Loose Screws: Tighten any loose screws using a screwdriver.
- Inspect the Handle Gasket: Replace if worn out. A worn gasket can cause the handle to stick.
- Lubricate the Handle: Apply a small amount of plumber’s grease. This helps the handle move smoothly.
If the handle remains loose or continues to stick, you might need to replace it.
Handle Replacement Process
Sometimes, replacing the handle is the best solution. Follow these steps to replace the handle:
- Turn Off Water Supply: Locate the shut-off valve and turn it off.
- Remove the Old Handle: Unscrew the handle from the flush valve. Use a wrench if needed.
- Install the New Handle: Align the new handle and secure it with screws.
- Turn On Water Supply: Open the shut-off valve and test the new handle.
Ensuring the handle is properly installed will keep the flush valve functioning correctly.
By following these simple steps, you can fix common handle issues. Keep your Sloan flush valve in optimal condition.
Advanced Sloan Flush Valve Troubleshooting Techniques
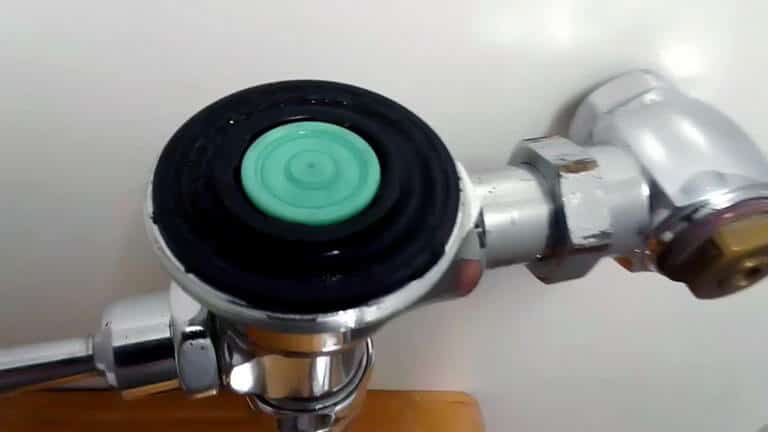
Advanced troubleshooting techniques can save time and effort when dealing with Sloan Flush Valve issues. These methods ensure your system runs smoothly and efficiently. Let’s explore some of these advanced techniques.
Vacuum Breaker Assessment
Start by checking the vacuum breaker for any signs of wear or damage. A faulty vacuum breaker can cause leakage or ineffective flushing. Inspect the breaker for cracks or debris. Use a flashlight to get a clear view.
Next, clean the vacuum breaker thoroughly. Dirt or mineral deposits can block its function. Soak the parts in a vinegar solution to remove buildup. Reassemble the parts carefully, ensuring each piece fits snugly.
If the vacuum breaker is beyond repair, replace it with a new one. Make sure to use genuine Sloan parts for the best performance.
Tailoring Solutions For Sensor-operated Valves
Sensor-operated valves require special attention. Ensure the sensor is free from obstructions. Dust or grime can interfere with its operation. Clean the sensor with a soft cloth and mild cleaner.
Check the sensor’s power supply. Ensure the batteries are fresh. Replace them if needed. If the valve is hardwired, inspect the connections for any loose or damaged wires.
Next, test the sensor’s range and sensitivity. Adjust these settings according to the manufacturer’s guidelines. Use a small screwdriver to tweak the settings until the sensor responds accurately.
Issue | Solution |
---|---|
Sensor not detecting users | Clean sensor and adjust sensitivity |
Weak flush | Check battery or power supply |
Continuous flushing | Inspect and clean the sensor |
Using these advanced troubleshooting techniques can greatly improve the performance of your Sloan Flush Valve. Regular maintenance and timely repairs ensure long-lasting functionality.
When To Call A Professional
Dealing with Sloan Flush Valve issues can be tricky. Minor problems can often be fixed with simple adjustments. But some issues need a professional’s touch. Understanding when to call for expert help can save time and money.
Recognizing Complex Issues
Some flush valve problems are easy to spot. They might include constant running water or a weak flush. But more complex issues can go unnoticed. Here are signs that indicate it’s time to call a professional:
- Water leaks around the valve or toilet base
- Unusual noises during flushing
- Inconsistent water flow
- Frequent need for repairs
These issues often point to bigger problems. A professional can diagnose and fix them correctly.
Finding Qualified Technicians
It’s important to find the right technician for the job. Look for licensed plumbers with experience in Sloan Flush Valves. Here are tips to find a qualified technician:
- Check online reviews and ratings
- Ask for recommendations from friends or family
- Verify licenses and certifications
- Get multiple quotes to compare prices
Qualified technicians can handle complex issues efficiently. They ensure your flush valve works perfectly.
Problem | DIY | Call Professional |
---|---|---|
Running Water | Check and clean the valve | If persists, call a plumber |
Weak Flush | Adjust the flush valve | If no improvement, seek help |
Leaks | Replace seals | If leaks continue, get professional advice |
Knowing when to call a professional is crucial. It ensures your Sloan Flush Valve works without issues.
Maintaining Your Sloan Flush Valve
Proper maintenance of your Sloan flush valve ensures a long lifespan. Regular upkeep reduces issues and keeps your restroom in top shape. Follow these simple steps for effective maintenance.
Regular Maintenance Tips
- Check for Leaks: Inspect the valve regularly for any signs of leakage.
- Clean the Diaphragm: Clean the diaphragm to prevent debris build-up.
- Inspect the Handle: Ensure the handle functions smoothly and replace if needed.
- Flush Test: Perform a flush test to make sure everything works perfectly.
Longevity Practices For Flush Valves
Action | Frequency |
---|---|
Professional Inspection | Annually |
Diaphragm Replacement | Every 2 Years |
Valve Lubrication | Every 6 Months |
Implementing these practices ensures your Sloan flush valve lasts longer. Consistent attention and care are key for optimal performance.
Frequently Asked Questions
How Do I Fix A Leaking Sloan Flush Valve?
First, check the diaphragm and replace any worn parts.
Why Is My Sloan Flush Valve Not Flushing?
A clogged or damaged diaphragm can prevent flushing. Clean or replace it to restore function.
What Causes A Sloan Flush Valve To Run Continuously?
A worn diaphragm or faulty handle assembly can cause continuous running. Inspect and replace if necessary.
How Do I Adjust A Sloan Flush Valve?
Turn the control stop screw counterclockwise to increase flow or clockwise to decrease flow.
Why Is My Sloan Flush Valve Making Noise?
Noise is often due to a loose diaphragm or debris. Tighten or clean to resolve the issue.
Conclusion
Troubleshooting a Sloan flush valve can seem daunting, but it’s manageable. Follow our tips for efficient fixes. Regular maintenance ensures long-lasting performance. Don’t ignore minor issues; they can escalate. Keep your restroom functioning smoothly by addressing problems promptly. Happy troubleshooting and keep your Sloan flush valves in top shape!